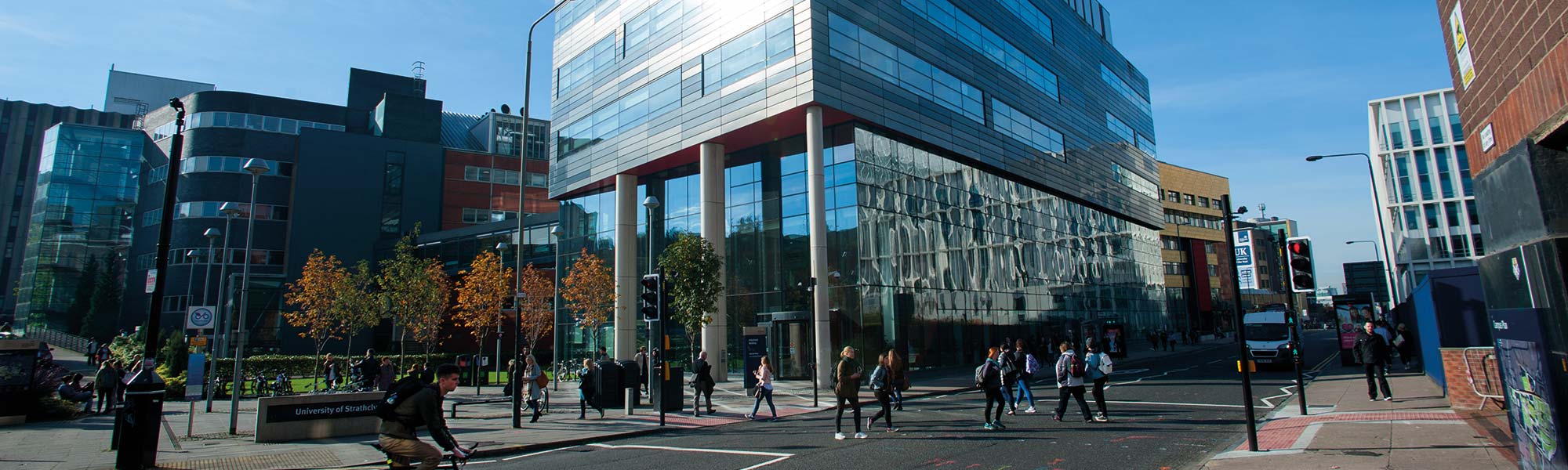
Dr Iain Burns
Senior Lecturer
Chemical and Process Engineering
Area of Expertise
I lead research on the development and application of custom measurement techniques for imaging reacting flows, including under harsh conditions of luminosity, turbidity and high temperature. This includes measurement of:
- Temperature
- Concentration of trace gases
- Concentration of particulates
- Particle size
This has obvious relevance to a wide range of industrial problems and we are keen to build new partnerships to exploit these possibilities.
Qualifications
MEng Chemical Engineering (University of Strathclyde)
PhD Chemical Engineering (University of Cambridge)
Publications
- Investigation of the effect of hydrogen addition on soot and PAH formation in ethylene inverse diffusion flames by combined LII and PAH LIF
- Ezenwajiaku Chinonso, Roy Robert Gray, Talibi Midhat, Balachandran Ramanarayanan, Burns Iain
- Fuel Vol 361 (2024)
- https://doi.org/10.1016/j.fuel.2023.130613
- Measurement of acetylene concentration in laminar flat flames by diode laser cavity ring-down spectroscopy
- Otti P, Humphries GS, Hu Y, Lengden M, Burns IS
- Applied Physics B: Lasers and Optics Vol 128 (2022)
- https://doi.org/10.1007/s00340-022-07883-y
- In-situ photoacoustic measurement of soot profiles in laminar flames using a high repetition-rate pulsed fibre laser
- Humphries Gordon S, Roy Robert, Black John D, Lengden Michael, Burns Iain S
- Applied Physics B: Lasers and Optics Vol 125 (2019)
- https://doi.org/10.1007/s00340-019-7169-0
- Alternative soot detection strategies for application in aero-engine test-beds : assessment of the performance and uncertainties of time-integrated LII
- Roy R, Blount C, Ramesh G, Ozanyan K, Wright P, Archilla V, Burns IS
- 9th European Combustion Meeting, pp. 1-5 (2019)
- CIDAR project - development of a non-intrusive capability for aircraft engine measurements
- Archilla V, Aragón G, Wright P, Ozanyan K, Black J, Lengden M, Burns I, Johnstone W, Polo V, Beltran M, Johnson M
- Aerosol Technology (2018)
- CIDAR : combustion species imaging diagnostics for aero-engine research
- Archilla V, Aragón G, Wright P, Ozanyan K, Black J, Polydorides N, McCann H, Lengden M, Burns I, Johnstone W, Polo V, Beltran M, Mauchline I, Walsh D, Johnson M
- Aerosol Technology (2018)
Teaching
I currently teach mass transfer, vapour-liquid separations and adsorption processes to Year 3 and process measurements to final year MEng students.
I supervise research and industrial projects for full-time and distance-learning MEng and MSc students, chemical engineering design projects and undergraduate summer research projects.
I have previously lectured on process design, engineering maths, thermodynamics and chemical reactor engineering so I have broad experience of teaching the core components of the Chemical Engineering undergraduate curriculum.
Research Interests
- Laser induced fluorescence
- Cavity ring-down spectroscopy
- Laser induced incandescence
- Light scattering
- Combustion
- Laminar flames
- Temperature measurement
- Trace gas detection
- Soot and polycyclic aromatic hydrocarbons
- Direct flame fuel cells
- Crystallisation
Professional Activities
- Strathclyde Adsorption Summer School 2024
- Keynote/plenary speaker
- 11/6/2024
- Strathclyde Adsorption Summer School 2023
- Keynote/plenary speaker
- 13/6/2023
- Strathclyde Adsorption Summer School 2022
- Keynote/plenary speaker
- 15/6/2022
- Strathclyde Adsorption Summer School 2019
- Keynote/plenary speaker
- 18/6/2019
- Strathclyde Adsorption Summer School 2018
- Keynote/plenary speaker
- 12/6/2018
- Strathclyde Adsorption Summer School 2017
- Keynote/plenary speaker
- 19/6/2017
Projects
- A Spectroscopy Suite for Direct Low Waste Measurement for All States of Matter
- Campbell, Andrew John (Principal Investigator) Burns, Iain (Co-investigator) Lengden, Michael (Co-investigator) Murray, Paul (Co-investigator)
- 01-Jan-2024 - 31-Jan-2024
- Doctoral Training Partnership 2020-2021 University of Strathclyde | Seecharam, Anshul Nilesh
- Burns, Iain (Principal Investigator) Brightman, Edward (Co-investigator) Seecharam, Anshul Nilesh (Research Co-investigator)
- 01-Jan-2022 - 01-Jan-2025
- Laser Imaging of Turbine Engine Combusion Species (LITECS) (Programme Grant)
- Lengden, Michael (Principal Investigator) Burns, Iain (Co-investigator) Johnstone, Walter (Co-investigator)
- 01-Jan-2020 - 28-Jan-2026
- AFRC_CATP_1216_RTI Application of TDLAS for gas monitoring
- Andreu, Aurik (Principal Investigator) Wilson, David (Academic) Burns, Iain (Principal Investigator)
- 31-Jan-2018 - 24-Jan-2019
- CIDAR for CleanSky 2 (Combustion species Imaging Diagnostics for Aero-engine Research)
- Lengden, Michael (Principal Investigator) Burns, Iain (Co-investigator) Johnstone, Walter (Co-investigator)
- 01-Jan-2018 - 31-Jan-2021
- 2016 EPSRC Doctoral Prize - Intra-Cavity Photo-acoustic Gas Sensing
- Humphries, Gordon Samuel (Principal Investigator) Lengden, Michael (Academic) Burns, Iain (Academic)
- The monitoring of trace gases at low concentration is of vital importance across a range of areas (pollutant emission measurement, process control, medical diagnostics). NOx pollution has attracted significant attention, due to the increase in diesel and nitrogen-based bio-fuels usage and the misrepresentation of pollutant levels in the automotive industry. This project will develop a highly sensitive optical sensor targeting nitric oxide (NO), which is an atmospheric pollutant and a pre-cursor to NO2, contributing to significant numbers of UK deaths per annum. Current measurement techniques cannot accurately measure NO and NO2 concentration in the atmosphere at the levels considered dangerous. As its harmful effects become increasingly apparent there is a pressing need for a step change in sensor technology, requiring two orders of magnitude improvement in sensitivity to levels lower than 500 parts per trillion (ppt) and providing improved data for analysis of pollutant species in environmental modelling.
To meet this need we will combine research from Strathclyde and Oxford University to develop a novel gas sensor, integrating the world-leading expertise from both institutions; Strathclyde- considerable expertise in cavity-based optical absorption and photoacoustic techniques for gas detection; Oxford – expertise in an advanced optical technique (optical-feedback-cavity- enhanced absorption spectroscopy - OF-CEAS). The integration of these two techniques has the potential to provide a sensitivity increase of two orders of magnitude, which translates to minimum detection sensitivities of NO and NO2 of 50ppt and 5ppt respectively, well within the range required for practical applications. - 01-Jan-2017 - 28-Jan-2018
Contact
Dr
Iain
Burns
Senior Lecturer
Chemical and Process Engineering
Email: iain.burns@strath.ac.uk
Tel: 548 4837