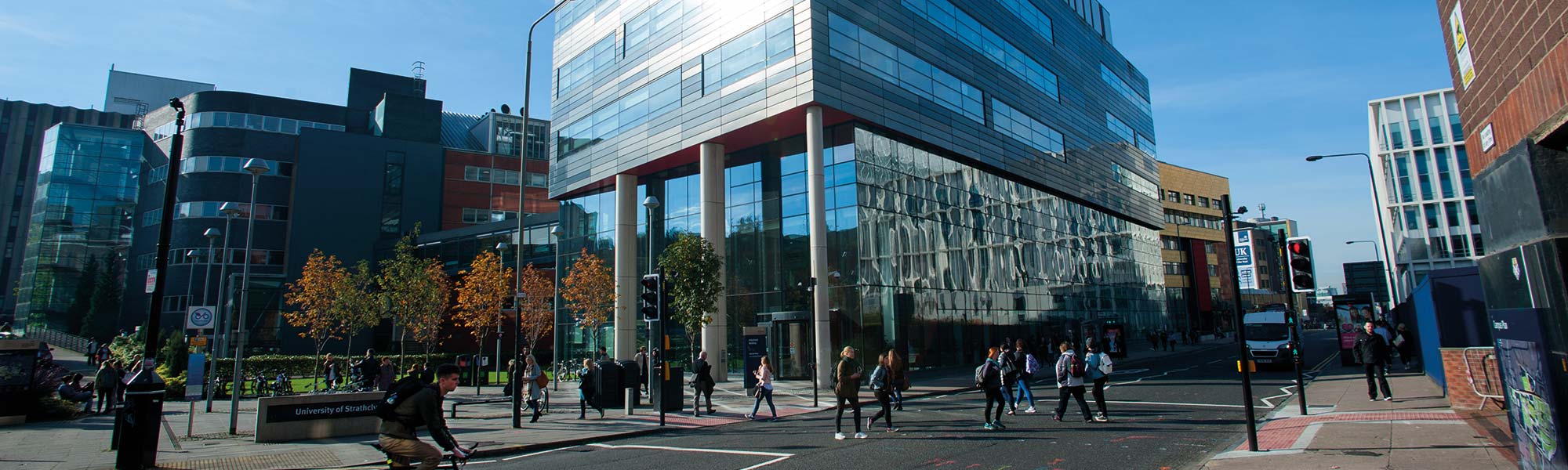
Dr Yevgen Gorash
Research Fellow
Mechanical and Aerospace Engineering
Back to staff profile
Area of Expertise
Software:
- CAD (SolidWorks, PTC Creo);
- CAE (ANSYS, ABAQUS, COMSOL, SolidWorks Simulation);
- Fatigue postprocessor (nCode DesignLife);
- Metal casting simulation (SolidCast, LVMFlow);
- Data analysis and mathematics (MathCAD, Maple, Matlab, OriginPro);
- Application development using API for CAD/CAE systems;
- Scientific reporting using TeX typesetting system (LaTeX, MiKTeX).
Expertise:
- Ultrasonic Fatigue Testing (using Shimadzu USF-2000a machine);
- Nonlinear material models (Plasticity and Viscoplasticity, Creep, Fatigue, Hyperelasticity, Unified material models)
- Finite Element Analysis; Continuum Damage Mechanics; Creep or/and Fatigue residual life assessment; Limit / shakedown and ratchetting analyses
Back to staff profile
Publications
- Development of laser AM process to repair damaged super duplex stainless steel components
- Ahmad Abdul, Xirouchakis Paul, Pearson Alastair, Brownlie Frazer, Gorash Yevgen
- Sustainability Vol 17 (2025)
- https://doi.org/10.3390/su17125438
- Assessing the very high cycle fatigue behaviour and frequency effect of structural steel welds
- England Andrew, Gorash Yevgen, Toumpis Athanasios
- Fatigue and Fracture of Engineering Materials and Structures Vol 48, pp. 1529-1541 (2025)
- https://doi.org/10.1111/ffe.14569
- Comparative fatigue analysis of structural steels considering welding and surface effects
- Gorash Yevgen, Comlekci Tugrul, Walker Carl, Toumpis Athanasios, Kelly James, England Andrew, Milne Lewis
- Strain Vol 61 (2025)
- https://doi.org/10.1111/str.70003
- Calibration of the DEM sliding friction and rolling friction parameters of a cohesionless bulk material
- Marin Perez Jonatan Emanuel, Comlekci Tugrul, Gorash Yevgen, MacKenzie Donald
- Particuology Vol 92, pp. 126-139 (2024)
- https://doi.org/10.1016/j.partic.2024.05.003
- Specimen design for gigacycle fatigue testing of structural steel welded joints
- England Andrew, Toumpis Athanasios, Gorash Yevgen
- Procedia Structural Integrity Vol 57, pp. 494-501 (2024)
- https://doi.org/10.1016/j.prostr.2024.03.054
- Application of finite-life frequency sensitivity evaluation methods to UFT of ferritic structural steels
- Milne Lewis Andrew, Gorash Yevgen, Comlekci Tugrul, MacKenzie Donald
- Fatigue Design 2023, pp. 365-374 (2024)
- https://doi.org/10.1016/j.prostr.2024.03.039
Back to staff profile
Research Interests
- Ultrasonic Fatigue Testing;
- Residual Life Assessments (based on fatigue and creep);
- Finite Element Analysis (CAE/FEA);
- Continuum Damage Mechanics (CDM);
- Rigid (Multi-)Body Dynamics.
Current research interests comprise study and modelling of non-linear material behaviour: Plasticity and Viscoplasticity, Creep, Fatigue, Hyperelasticity, Unified material models. These non-linear material effects are applied to the residual life assessments of engineering structures subject to severe loading conditions using FEA and concepts of Continuum Damage Mechanics.
Projects
- Development of Sustainable Mining Equipment using Novel Fracture Mechanics based Structural Design Optimisation SRSS REA 2725 WARC International PhD Student
- Comlekci, Tugrul (Principal Investigator) Gorash, Yevgen (Co-investigator) MacKenzie, Donald (Co-investigator)
- 01-Jan-2023 - 31-Jan-2026
- Doctoral Training Partnership (DTP 2016-2017 University of Strathclyde) | Connolly, Stephen
- MacKenzie, Donald (Principal Investigator) Gorash, Yevgen (Co-investigator) Connolly, Stephen (Research Co-investigator)
- 01-Jan-2016 - 22-Jan-2020
- Design optimisation of of swellable elastomeric seals using advanced material modelling and FEM simulations with HPC
- Gorash, Yevgen (Principal Investigator) Bickley, Alan (Administrator) Gozalo, Francisco (Co-investigator)
- Swellable elastomeric seals (packers) have been widely employed in various oil-&-gas and minerals applications. Examples include slimming of well design, zonal isolation, water shut-off, and multi-stage fracturing. Important characteristics of packers required for these applications are how fast the packer can seal the borehole as well as how fast a certain amount of contact pressure can build up. These characteristics, which are generally measured from full-scale packer tests, can be predicted through numerical FEM simulations (using ABAQUS, ANSYS, MSC.Marc etc.) based on material data obtained from basic experiments. The key component of numerical prediction is an availability of advanced material models for swellable elastomers, which would be capable of accurate simulation of packers’ non-linear mechanical behaviour under various downhole conditions. The numerical simulation of packers can be incorporated into optimisation procedure finding an optimal shape of packers with the goals to minimise the time to seal the borehole and maximise the contact pressure between the seal and borehole. Such an optimisation procedure would allow the Weir Group to produce the packer with various designs optimised for different downhole conditions considering the borehole type, i.e., permeable or non-permeable borehole, and downhole uncertainties, i.e., variations of borehole size and borehole temperature. Through this research project, we hope to develop an optimisation procedure based on advanced FEM simulation to provide us an improved design of packers produced by Weir Minerals USA and design recommendations for various downhole conditions.
- 01-Jan-2016 - 31-Jan-2018
- Project 3.7: Investigation and model development of valve leak tightness
- Anwar, Ali (Post Grad Student) Gorash, Yevgen (Research Co-investigator) Dempster, William (Principal Investigator) Hamilton, Robert (Academic) Nash, David (Academic)
- Pressure Relief Valves (PRV) tend to leak at high pressures. Customers demand a guarantee of leak tightness as a percentage of the set pressure. WEIR competitors can guarantee a higher leak tightness and therefore in certain circumstance we lose orders to our competitors. This work program is intended to understand why PRV's leak and how to reduce or mitigate against the leakage. Improving WEIR design will support the sale of more product. The main purpose of this research is to deliver prediction methods for sealing design with specific emphasis on Weir Group Sarasin-RSBD valve products.
The main objective of this problem is to be able to re-create this leakage issue using computational tools. This will be done using a combination of Finite Element Analysis (FEA) and Computational Fluid Dynamics (CFD). The complexities of this research lie with the deformation and surface effects of the "sealing faces" of the valves at a micron and macro scale including load cycling and creep behaviour analysis. This has to be analysed and reproduced at corresponding pressures and temperatures with compressible or incompressible fluid flow using combined FEA and CFD tools. - 24-Jan-2014 - 24-Jan-2017
- WeirSPM Pump of the Future PowerFrame
- Gorash, Yevgen (Researcher) Comlekci, Tugrul (Principal Investigator) MacKenzie, Donald (Academic)
- The design for the POTF is currently being completed by Weir SPM and based on
the discussions on the new design, a set of numerical analysis studies are now proposed for the powerframe of the POTF:
• Kinematic analysis,
• Structural analysis,
• Fatigue analysis,
• Design variations and optimisation analysis. - 01-Jan-2014 - 31-Jan-2014
- Material modelling and numerical simulation of elastomeric components in pumps and valves
- Gorash, Yevgen (Researcher) Comlekci, Tugrul (Principal Investigator) Hamilton, Robert (Academic)
- Objectives include:
1. Develop an FEA based methodology and procedure that local Weir Group engineering sites can use to better analyse and predict the behaviour of elastomeric components.
2. Develop an understanding into the behaviour of elastomeric materials in Weir Group products, components and manufacturing issues.
3. Develop a training program on elastomer modelling for Weir Group Engineers. - 01-Jan-2013 - 31-Jan-2014
Back to staff profile
Contact
Dr
Yevgen
Gorash
Research Fellow
Mechanical and Aerospace Engineering
Email: yevgen.gorash@strath.ac.uk
Tel: Unlisted