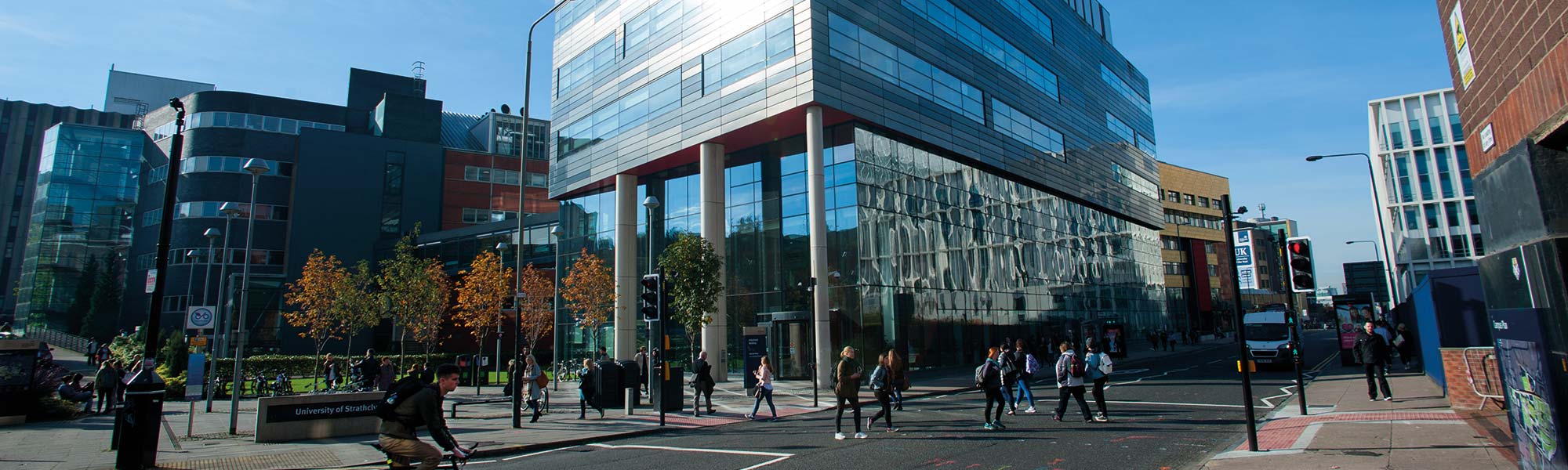
Professor David Nash
Mechanical and Aerospace Engineering
Back to staff profile
Area of Expertise
- Finite element analysis
- Mechanical structural design
- Pressure Vessels and piping systems
- Bio-mechanics
- CPD
- Stress analysis in all its forms - ANSYS and ABAQUS
- Design and optimisation of engineering structures
- Use of codes and standards and design by analysis
- Design of medical devices
Back to staff profile
Publications
- Development of a test rig for improved estimation of structural damping of wind turbine composite materials
- Brough Euan, Nash David, Kazemi Amiri Abbas Mehrad, Couturier Philippe, Reis Vitor Luiz
- Proceedings of ASME 2023 Aerospace Structures, Structural Dynamics, and Materials Conference, SSDM 2023 ASME 2023 Aerospace Structures, Structural Dynamics, and Materials Conference Proceedings of ASME 2023 Aerospace Structures, Structural Dynamics, and Materials Conference, SSDM 2023 (2023)
- https://doi.org/10.1115/SSDM2023-108462
- Stress linearization application of oblique nozzles with welded pad reinforcement in cylindrical pressure vessels
- Bozkurt Murat, Nash David
- Proceedings of the Institution of Mechanical Engineers, Part C: Journal of Mechanical Engineering Science Vol 238, pp. 1642-1654 (2023)
- https://doi.org/10.1177/09544062231187726
- Influence of heat treatments on the microstructure and mechanical properties of two fine Mg-Li-Y alloy wires for bioresorbable applications
- Macleod Kenneth, Nash David h, Bow David r, Ma Le
- Advanced Engineering Materials Vol 25 (2023)
- https://doi.org/10.1002/adem.202201164
- A novel approach for wind turbine blade erosion characterization : an investigation using surface gloss measurement
- Leishman Grant, Nash David, Yang Liu, Dyer Kirsten
- Coatings Vol 12 (2022)
- https://doi.org/10.3390/coatings12070928
- A comparison of stress analysis and limit analysis approaches for single and multiple nozzle combinations in cylindrical pressure vessels
- Bozkurt Murat, Nash David, Uzzaman Asraf
- International Journal of Pressure Vessels and Piping Vol 194 (2021)
- https://doi.org/10.1016/j.ijpvp.2021.104563
- Calculation of outer crack stress intensity factors for nozzle junctions in cylindrical pressure vessels using FCPAS
- Bozkurt Murat, Nash David, Uzzaman Asraf
- Proceedings of the ASME 2021 Pressure Vessels & Piping Conference ASME 2021 Pressure Vessels & Piping Conference Volume 2: Computer Technology and Bolted Joints; Design and Analysis (2021)
- https://doi.org/10.1115/PVP2021-64385
Back to staff profile
Research Interests
Applications of finite element analysis:
- specifically pressure vessels and piping,
- bio-mechanics,
- materials
Projects
- ICF Mechanical Property Optimisation of Magnesium Alloy Wires for Bio-resorbable Vascular Scaffolds for the treatment of Peripheral Arterial Disease
- Nash, David (Principal Investigator)
- 01-Jan-2024 - 31-Jan-2025
- Minimising the implantation size of a novel bioresorbable vascular scaffold through optimising the microstructure and mechanical properties of a novel magnesium alloy (AKT)
- Nash, David (Principal Investigator)
- 01-Jan-2022 - 31-Jan-2023
- IAA - Irregular anatomical effects on fatigue safety and sealing performance of stent grafts
- Nash, David (Principal Investigator) Dempster, William (Co-investigator)
- 01-Jan-2019 - 31-Jan-2019
- Boiler Technologies - Strucutural and Thermal Aspects
- Nash, David (Principal Investigator) Dempster, William (Co-investigator)
- 01-Jan-2018 - 30-Jan-2018
- Doctoral Training Partnership (DTP 2016-2017 University of Strathclyde) | Kucharek, Mariusz
- Yang, Liu (Principal Investigator) Nash, David (Co-investigator) Kucharek, Mariusz (Research Co-investigator)
- 01-Jan-2017 - 23-Jan-2022
- Nitinol Complex Loads
- Wheel, Marcus (Principal Investigator) Nash, David (Co-investigator)
- 18-Jan-2017 - 17-Jan-2020
Back to staff profile
Contact
Professor
David
Nash
Mechanical and Aerospace Engineering
Email: d.nash@strath.ac.uk
Tel: 548 2313