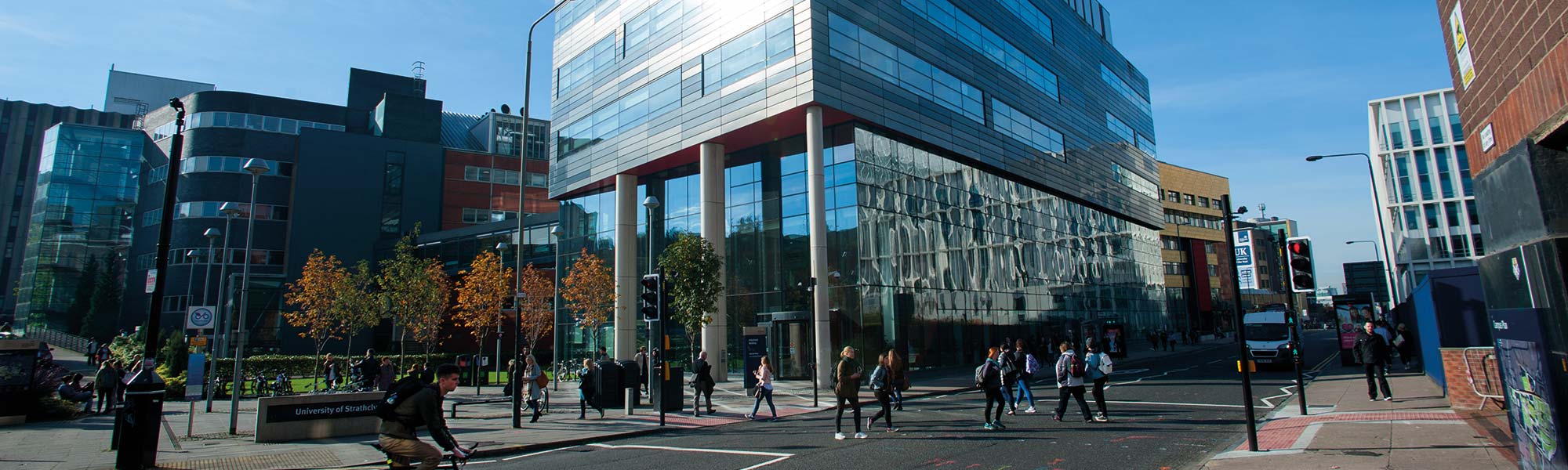
Professor Salaheddin Rahimi
Professor Of Practice
Advanced Forming Research Centre
Back to staff profile
Prize And Awards
- Fellow of The Institute of Materials, Minerals and Mining
- Recipient
- 9/2018
- A Freeman Citizen of Glasgow
- Recipient
- 4/2018
- Managing Safety
- Recipient
- 4/2018
- Professional Member of The Institute of Materials, Minerals and Mining
- Recipient
- 11/2016
- Charted Engineer (C.Eng)
- Recipient
- 11/2016
- Team Leading Award
- Recipient
- 2015
Back to staff profile
Publications
- Sustainable manufacturing of a high-value tubular Ti-6Al-4V component using flow-forming process; effect of feed-rate on microstructure evolution
- Banerjee Amborish, Nelson Kyle, Roszak Jacob, Paslioglu Kadir, Sivaswamy Giribaskar, da Silva Laurie, Rahimi Salah
- Materials Chemistry and Physics Vol 344 (2025)
- https://doi.org/10.1016/j.matchemphys.2025.131086
- Modelling and measurements of thermally induced residual stress in IN718 nickel-based superalloy during non-uniform quenching
- Rahimi Salah, King Michael, Amir Siddiq Muhammad, Wynne Bradley
- Materials and Design Vol 250 (2025)
- https://doi.org/10.1016/j.matdes.2025.113615
- Numerical modelling of the water-quenching process validated through experiments with IN718 nickel-based superalloy
- Kamenicky Robin, Rahimi Salaheddin, Violatos Ioannis, Ritos Konstantinos
- International Journal of Heat and Mass Transfer Vol 235 (2024)
- https://doi.org/10.1016/j.ijheatmasstransfer.2024.126158
- Miniaturised experimental simulation and combined modelling of open-die forging of Ti-6Al-4V titanium alloy
- Connolly David, Fabris Mathieu, Sivaswamy Giribaskar, Rahimi Salah, Vorontsov Vassili
- Journal of Materials Research and Technology Vol 30, pp. 3622-3639 (2024)
- https://doi.org/10.1016/j.jmrt.2024.04.084
- Predicting fatigue crack initiation in milled aerospace grade Ti-6Al-4V parts using CPFEM
- Arcidiacono Mauro Francisco, Violatos Ioannis, Rahimi Salaheddin
- Proceedings of the 9th Engineering Integrity Society International Conference on Durability & Fatigue 9th Engineering Integrity Society International Conference on Durability & Fatigue (Fatigue 2024), pp. 115-126 (2024)
- https://doi.org/10.5281/zenodo.12705102
- Optimisation of sample geometry for thermo-mechanical testing of precipitation hardenable nickel-based superalloys with an ETMT machine
- King Michael, Rahimi Salah
- Strain Vol 60 (2024)
- https://doi.org/10.1111/str.12458
Back to staff profile
Professional Activities
- PhD Viva - Applying the contour method of residual stress measurement to irregular components
- Examiner
- 28/2/2024
- 17th International Conference on Advances in Experimental Mechanics
- Keynote/plenary speaker
- 30/8/2023
- World Titanium Conference 2023
- Keynote/plenary speaker
- 12/6/2023
- 17th International Conference on Engineering StructuralIntegrity Asessment(ESIA17)
- Keynote/plenary speaker
- 23/5/2023
- Establishing a mechanism-based constitutive model for simulating superplastic forming in a near-α TA15 titanium alloy
- Speaker
- 12/5/2023
- PhD Viva
- Examiner
- 30/3/2023
Projects
- Comparative Analysis of Residual Stresses in Aluminum Components Produced by Wire Arc Additive Manufacturing (WAAM) and AdditiveFriction Stir Deposition (AFSD)
- Javadi, Yashar (Principal Investigator) MacLeod, Charles Norman (Co-investigator) BUFFA, GIANLUCA (Co-investigator) Tamimi, Saeed (Co-investigator) Rahimi, Salaheddin (Co-investigator) Paradowska, Anna (Co-investigator) Alipooramirabad, Houman (Co-investigator)
- This collaborative study between ANSTO, University of Palermo, University of Strathclyde, and AFRC investigates residual stresses in aluminum components produced via WAAM and AFSD (including MELD). Using neutron diffraction and ultrasonic techniques, the project aims to characterize and compare stress profiles across processes. The findings will inform process optimization and contribute to a doctoral thesis on in-situ stress measurement in metal additive manufacturing.
- 10-Jan-2025 - 09-Jan-2026
- Marine Vessel Lightweighting (MARILIGHT) Lead_06847
- Rahimi, Salaheddin (Principal Investigator)
- 01-Jan-2023 - 30-Jan-2023
- Robotic Ultrasonic System for In-situ Residual Stress Measurement in Metal Additive Manufacturing
- Walker, Joseph (Post Grad Student) Javadi, Yashar (Principal Investigator) Heidari, Hadi (Co-investigator) Rahimi, Salaheddin (Co-investigator)
- Residual Stress (RS) in engineering components yields unexpected and dangerous structural failures, and thus represents a significant challenge to quality assurance in both welding and metal Additive Manufacturing (AM) processes. As automation in welding and AM becomes increasingly prevalent in the Industry 4.0 manufacturing paradigm, so the importance of quantifying RS will grow. In this PhD project, a novel robotic ultrasonic approach to measuring such RS, in-situ, will be developed using the Phased Array Ultrasonic Testing (PAUT) system, to automate the deployment of the measurement in manufacturing applications. For the first time, it will allow truly in-situ measurements of RS to be undertaken at the elevated temperatures associated with welding and metal AM manufacture. The ambition is to use this in-situ measurement system for safety-critical and Industry 4.0 applications, through 5G wireless integration of the robotic system, where the conventional manual and destructive methods of RS measurement are not applicable for high throughput and automated production lines.
- 01-Jan-2022 - 30-Jan-2026
- Doctoral Training Partnership 2020-2021 University of Strathclyde | Dogan, Gulsum
- Vorontsov, Vassili (Principal Investigator) Rahimi, Salaheddin (Co-investigator) Dogan, Gulsum (Research Co-investigator)
- 01-Jan-2022 - 01-Jan-2025
- AFRC_DIRF_1586
- Easton, David (Principal Investigator) Rahimi, Salaheddin (Co-investigator)
- 09-Jan-2021 - 30-Jan-2021
- AFRC_DIRF_1887
- Rahimi, Salaheddin (Principal Investigator)
- 11-Jan-2021 - 28-Jan-2021
Back to staff profile
Contact
Professor
Salaheddin
Rahimi
Professor Of Practice
Advanced Forming Research Centre
Email: salah.rahimi@strath.ac.uk
Tel: 534 5243