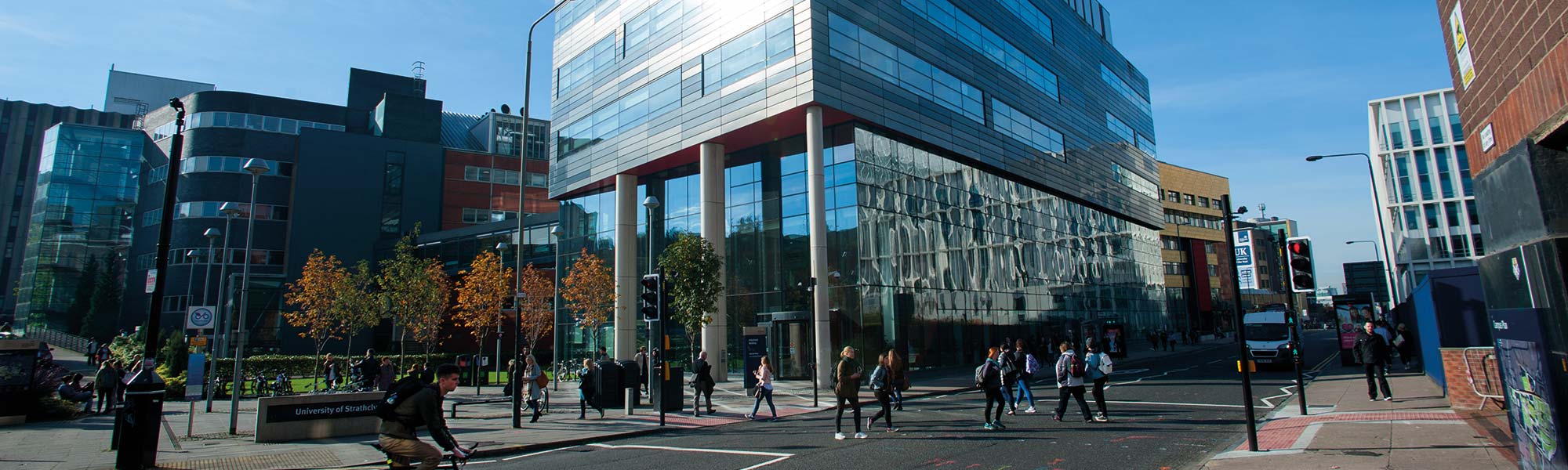
Dr Aurik Andreu
Heating Technologies Theme Lead
Advanced Forming Research Centre
Back to staff profile
Publications
- DIGF-PRS02623-DIRF06554-D1-Heating Trials Summary
- Jadhav Sandip, Elsayed Ahmed, Andreu Aurik
- (2024)
- Improving forging outcomes of cast titanium aluminide alloy via cyclic induction heat treatment
- Peters Sean, Andreu Aurik, Perez Marcos, Blackwell Paul
- Metals Vol 13 (2023)
- https://doi.org/10.3390/met13081420
- Enhancing process efficiency through improved temperature measurement : the EMPRESS projects
- Pearce J V, Edler F, Fateev A, Sutton G, Andreu A, Machin G
- Journal of Physics: Conference Series Vol 2554 (2023)
- https://doi.org/10.1088/1742-6596/2554/1/012003
- Imaging luminescence thermometry to 750 °C for the heat treatment of common engineering alloys and comparison with thermal imaging
- Sutton Gavin, Korniliou Sofia, Andreu Aurik, Wilson David
- International Journal of Thermophysics Vol 43 (2022)
- https://doi.org/10.1007/s10765-021-02963-1
- A novel cyclic thermal treatment for enhanced globularisation kinetics in Ti-6Al-4V alloy : experimental, constitutive and FE based analyses
- Souza Paul M, Sivaswamy Giribaskar, Andreu Aurik, Rahimi Salaheddin
- Journal of Alloys and Compounds (2021)
- https://doi.org/10.1016/j.jallcom.2021.162859
- Integrated self-validating thermocouples with a reference temperature up to 1329 °C
- Tucker Declan, Andreu Aurik, Elliott Claire, Ford Trevor, Neagu Marius, Machin Graham, Pearce Jonathan
- Measurement Science and Technology Vol 29 (2018)
- https://doi.org/10.1088/1361-6501/aad8a8
Back to staff profile
Professional Activities
- 2023 AFRC Intern project - Preliminary development of CFD models for combustion system
- Lecturer
- 1/6/2023
- 2019 AFRC Intern project - Induction heating project / Real-Time Signal Processing, Control, and Simulation
- Lecturer
- 1/6/2019
- 2018 AFRC Intern project - Oxidation & H2 Pick up inTi64 & Induction Heating
- Lecturer
- 1/6/2018
- 2017 AFRC Intern project - Emissivity Measurement Project
- Lecturer
- 1/6/2017
- International Conference on Carbon
- Participant
- 2009
- International Conference on Carbon
- Participant
- 2007
Projects
- Thermometry with embedded SI traceability for industrial applications
- Andreu, Aurik (Principal Investigator)
- Most industrial processes rely on temperature measurement, which directly influences product quality, energy efficiency, and emissions. All conventional temperature sensors exhibit calibration drift leading to inefficiencies. Poor surface thermometry causes process control problems in advanced manufacturing. Poor gas thermometry causes sub-optimal noxious emissions and reduced efficiency. This project will overcome specific process control challenges by implementing embedded traceable thermometry in situ through driftless practical primary thermometry and self-validation, gas/combustion thermometry, and new traceable surface temperature measurement methods. Traceability [1] will be either directly to the redefined SI kelvin [2], or indirectly via the International Temperature Scale of 1990 (ITS-90) [3].
- 01-Jan-2024 - 31-Jan-2027
- ThermoSI – Thermometry with embedded SI traceability for industrial applications
- Andreu, Aurik (Principal Investigator)
- 01-Jan-2024 - 31-Jan-2027
- CORE_06601_Heating Tech
- Andreu, Aurik (Principal Investigator) Chalkley, Eleanor (Co-investigator) Huang, Jianglin (Co-investigator)
- Furnace Efficiency
The work of CORE 06223 focused on tools for assessing and modelling the energy usage and efficiency of heating processes based around the AFRC’s CMI gas furnace. WP3 and WP4 in this project expands the scope of these tools and preparations for assessments to the gas and electrical furnaces that are part of the FutureForge cell.
The characteristics of heating processes in the FutureForge furnaces are to be measured and used to validate existing models. The archive of experimental data from previous years of CORE projects was used to produce a fast analytical model of the CMI gas furnace and develop a tool for calculating the energy balance across multiple modes of use. In order to be able to assess the relative merits of the gas and electrical furnaces, building and analysing a furnace data archive and exploring the parameter space of each furnace to produce effective models will be required.
Life Cycle Assessment (LCA) and carbon accounting processes are likely to be of increasing regulatory and financial importance and so setting up to be rigorous and accurate in these calculations is vital.
Induction Hardening
This project will focus on the simulation of induction heating / hardening process of a crankshaft by applying the knowledge and expertise developed in previous CORD projects sponsored by BIFRANGI (i.e., CORD 1137, CORD 1444, CORD 1844 and CORECORD 06093 projects) on induction heating modelling and temperature measurement improvement.
Following discussions with Bifrangi, due to the complexity of the induction hardening of crankshafts and due to technical capability of the available software, we have decided to use Transvalor Forge for this project.
We propose to apply the developed induction heating process model for simulating induction heating / hardening process carried out at BIFRANGI. By simulating the induction hardening process and comparing the simulation results with experimental results from induction hardened samples, the developed induction heating process model can be further improved and verified. We are planning to carry out numerical sensitivity study/calibration of key parameters (current density, frequency, heating time / exposure, speed, distance coil/part) in the 3D FEM model and also as indicated by Bifrangi, investigate an interesting feature of this induction hardening process, i.e., the modulation of the power during each rotation of the part to stop parts of the crank melting or cracking. The improved maturity of modelling capabilities of the induction heating process should provide valuable information for industrial process design and optimisation.
Following the rescoping exercise due to the unavailability of the FF furnaces, we have a added an additional Workpackage to evaluate the new version Deform V14.0 for the rack bar induction hardening (focusing on rack side).
Completion of this work package will allow us to check if the new functionalities of Deform are working as expected. These functionalities could prove very valuable to model efficiently and more easily dynamic induction hardening process and will place Deform together with Transvalor Forge as a software of choice for this type of process. It is also a very good way to continue collaboration with Wilde Analysis and developers to improve Deform software and performance. - 18-Jan-2023 - 15-Jan-2024
- DIGF-DIRF-06554_Experiment Design for the Heating of Metal Wind Turbine Bolt
- Jadhav, Sandip (Principal Investigator) Elsayed, Ahmed (Co-investigator) Andreu, Aurik (Co-investigator)
- 02-Jan-2023 - 29-Jan-2024
- AFRC_CORE_1732_CONTINUATION WORK ON H2 PICKUP IN TI ALLOYS PLUS PRESS TRIALS – OPTION 1
- Andreu, Aurik (Principal Investigator) Khismatullin, Timur (Researcher)
- This project is a continuation of work carried out within CORE 814 & 1138 – Gas Furnace Characterisation on the hydrogen pickup and alpha case characterisation on Ti alloy parts submitted to heat treatment in a gas fired furnace.
For this year’s CORD project, we want to put the emphasis on parts with various finishes (ground, cast, machined) and different coatings (ATP40 & Prince Minerals coating). Some of the cast samples will also be submitted to press trials to evaluate the coating resistance/structure after one pass similarly to the cogging process.
Post heating analysis of the parts will be used to determine the amount of hydrogen and the oxidation layer in the samples. This should help us to improve our knowledge on the hydrogen pickup phenomenon, alpha case formation on Ti64 alloy materials and the usefulness of coating.
This project will be mainly funded using some remaining TIMET votes from CORE 20/21 programme.
The AFRC’s proposed approach to this project is described below in a series of 2 individual work packages. - 01-Jan-2022 - 15-Jan-2023
- AFRC_CORD_06093_Bifrangi Simulation of Induction heating / hardening process
- Andreu, Aurik (Principal Investigator) Huang, Jianglin (Co-investigator)
- This project will focus on the simulation of the induction heating / hardening process by applying the knowledge and expertise developed in previous CORD projects sponsored by BIFRANGI (CORD 1137, CORD 1444 and CORD 1844 projects) on induction heating modelling and temperature measurement improvement.
In previous projects, the standard and best practice on modelling of induction heating process has been established and the induction heating process model has been verified using lab-scale induction heating trials without billet movement. In this year’s CORD 1844 project, a 3D FEM model has been developed in DEFORM and used to investigate the effect of billet shape, size and offset in BIFRANGI’s induction heating line. An attempt has been made to scale up a 3D FEM model with moving billets to simulate the full BIFRANGI induction heating line with a length of 18 meters using 3 coils and cyclic operation. However, due to some technical issues (difficulty to simulate the full billet and line length, current measurement of the induction heating line (still planned for this year), and internal temperature data), there is still limited experimental data for process model verification.
We propose to apply the developed induction heating process model for simulating induction heating / hardening process carried out at BIFRANGI. By simulating the induction hardening process and comparing the simulation results with experimental results from induction hardened samples, the developed induction heating process model can be further improved and verified. The improved maturity of modelling capabilities of the induction heating process will provide value information for industrial process design and optimisation.
Additionally, following discussions with the Transvalor team and Bifrangi, it was decided to that we will also try out the Transvalor software suite Forge / Simheat to model this induction heating / hardening process. This will include an advanced training on Forge in relation to the induction heating / hardening modelling. This will allow us to compare simulation results with experimental trials and make sure both models in DEFORM and Transvalor are reliable and assess each set of software capabilities related to the induction heating/hardening process. - 01-Jan-2022 - 01-Jan-2023
Back to staff profile
Contact
Dr
Aurik
Andreu
Heating Technologies Theme Lead
Advanced Forming Research Centre
Email: aurik.andreu@strath.ac.uk
Tel: 534 5572