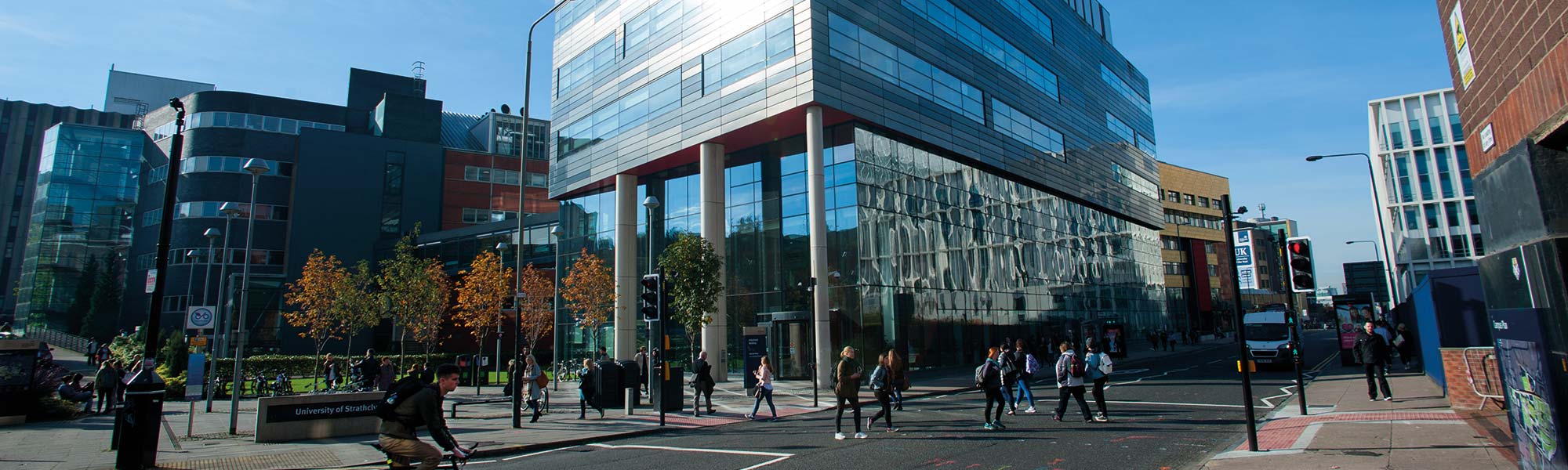
Dr Eleanor Chalkley
Senior Manufacturing Engineer
Advanced Forming Research Centre
Back to staff profile
Professional Activities
- Strategic Themes - IEEE Distinguished Lecture Series – GE Gas Measurement Sensor Technologies
- Participant
- 26/11/2024
Projects
- CORE_06601_Heating Tech
- Andreu, Aurik (Principal Investigator) Chalkley, Eleanor (Co-investigator) Huang, Jianglin (Co-investigator)
- Furnace Efficiency
The work of CORE 06223 focused on tools for assessing and modelling the energy usage and efficiency of heating processes based around the AFRC’s CMI gas furnace. WP3 and WP4 in this project expands the scope of these tools and preparations for assessments to the gas and electrical furnaces that are part of the FutureForge cell.
The characteristics of heating processes in the FutureForge furnaces are to be measured and used to validate existing models. The archive of experimental data from previous years of CORE projects was used to produce a fast analytical model of the CMI gas furnace and develop a tool for calculating the energy balance across multiple modes of use. In order to be able to assess the relative merits of the gas and electrical furnaces, building and analysing a furnace data archive and exploring the parameter space of each furnace to produce effective models will be required.
Life Cycle Assessment (LCA) and carbon accounting processes are likely to be of increasing regulatory and financial importance and so setting up to be rigorous and accurate in these calculations is vital.
Induction Hardening
This project will focus on the simulation of induction heating / hardening process of a crankshaft by applying the knowledge and expertise developed in previous CORD projects sponsored by BIFRANGI (i.e., CORD 1137, CORD 1444, CORD 1844 and CORECORD 06093 projects) on induction heating modelling and temperature measurement improvement.
Following discussions with Bifrangi, due to the complexity of the induction hardening of crankshafts and due to technical capability of the available software, we have decided to use Transvalor Forge for this project.
We propose to apply the developed induction heating process model for simulating induction heating / hardening process carried out at BIFRANGI. By simulating the induction hardening process and comparing the simulation results with experimental results from induction hardened samples, the developed induction heating process model can be further improved and verified. We are planning to carry out numerical sensitivity study/calibration of key parameters (current density, frequency, heating time / exposure, speed, distance coil/part) in the 3D FEM model and also as indicated by Bifrangi, investigate an interesting feature of this induction hardening process, i.e., the modulation of the power during each rotation of the part to stop parts of the crank melting or cracking. The improved maturity of modelling capabilities of the induction heating process should provide valuable information for industrial process design and optimisation.
Following the rescoping exercise due to the unavailability of the FF furnaces, we have a added an additional Workpackage to evaluate the new version Deform V14.0 for the rack bar induction hardening (focusing on rack side).
Completion of this work package will allow us to check if the new functionalities of Deform are working as expected. These functionalities could prove very valuable to model efficiently and more easily dynamic induction hardening process and will place Deform together with Transvalor Forge as a software of choice for this type of process. It is also a very good way to continue collaboration with Wilde Analysis and developers to improve Deform software and performance. - 18-Jan-2023 - 15-Jan-2024
- FutureForge strategic programme
- Perez, Marcos (Principal Investigator) Reshetov, Aleksey (Research Co-investigator) Bylya, Olga (Fellow) McDonach, Alaster (Fellow) Khatuntseva, Anastasia (Researcher) Andreu, Aurik (Fellow) Fleming, Christopher (Fellow) Chalkley, Eleanor (Fellow) Falsafi, Javad (Principal Investigator) Huang, Jianglin (Fellow) Rosochowska, Malgorzata (Fellow) Khismatullin, Timur (Researcher) Liang, Sha (Researcher) Millar, Richard (Researcher)
- Aiming to further develop fundamental understanding in key areas related to closed die, open die and isothermal forging, and exploring promising new capabilities, such as process instrumentation & data control and lubrication & coatings for hot forging at high temperatures.Topic areas included: microstructural and process modelling, validation geometry, study of key process variables such as lubrication and coatings for hot die forging, quasi-isothermal forging, instrumentation and data control in addition to temperature control of billets in gas furnaces.
- 01-Jan-2019 - 31-Jan-2020
- AFRC_CORD_1137_Induction Heating
- Andreu, Aurik (Principal Investigator) Huang, Jianglin (Co-investigator) Chalkley, Eleanor (Co-investigator)
- Induction heating (IH) is used in many applications such as: surface hardening, pre-heating for forging/forming, assembly processes, metal/alloy fusion, etc. The primary attraction of this technology is that it offers relatively fast heating rates and due to its direct nature there is little loss of energy in raising the temperature of refractories or other extraneous objects. Thus, if it is applicable it represents an extremely cost effective method of heating. Moreover, advances in key technologies, i.e. power electronics, control techniques, and magnetic component design, have allowed the development of highly reliable and cost-effective systems, making this technology readily available and ubiquitous.
Although IH systems have reached certain maturity, there are still some issues to address to further increase its performance and a number of challenges, notably in its application to non-axisymmetric geometries and it controlling the temperature gradient in the workpiece.
This proposal focuses on examining the capability of commercial software to simulate this process and then developing a validated model. A proposed secondary area for research is the measurement of temperature during IH, particularly on scaled surfaces to deliver improved yield and reduced wastage.
The AFRC’s proposed approach to this project is described below in a series of individual work packages. Depending on member agreement the AFRC may seek an industrial IH supplier to partner on this project – examples might include Ajax Tocco, Inductelec (Sheffield), or Inductotherm (Cheltenham). For coil design the AFRC already has contacts with Induction Coil Solutions with whom it has worked in the past.
It is recognised that elements of this project may require the AFRC project team to liaise with colleagues in the Electrical and Electronic Engineering Department for support in carrying out measurements during trials and for possible simulation of circuit dynamics. - 11-Jan-2018 - 31-Jan-2019
- FutureForge - Validation geometry
- Perez, Marcos (Principal Investigator) Reshetov, Aleksey (Research Co-investigator) Bylya, Olga (Fellow) Easton, David (Fellow) Ntovas, Michail (Researcher) Fabris, Mathieu (Researcher) Falsafi, Javad (Researcher) Huang, Jianglin (Fellow) Rosochowska, Malgorzata (Fellow) Chalkley, Eleanor (Fellow)
- Develop fundamental understanding in key areas related related to open, close-die and isothermal forging, exploring promising new capabilities, such as ultrasonic non-destructive characterisation and process instrumentation and data control.
- 21-Jan-2018 - 31-Jan-2019
Back to staff profile
Contact
Dr
Eleanor
Chalkley
Senior Manufacturing Engineer
Advanced Forming Research Centre
Email: eleanor.chalkley@strath.ac.uk
Tel: 534 5518