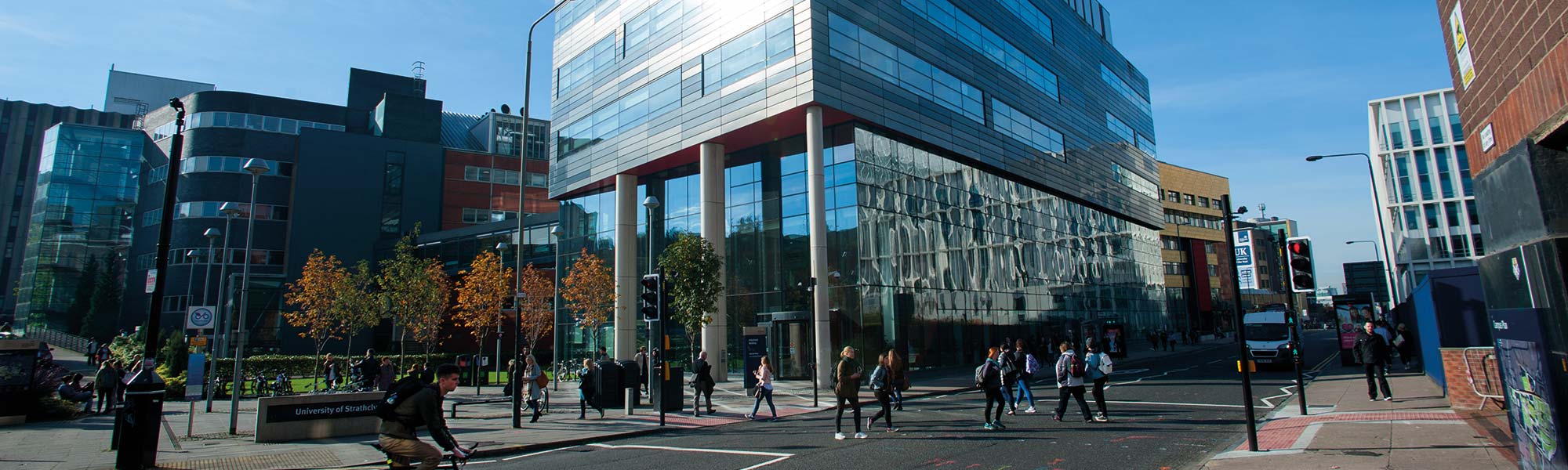
Professor Bill Ion
Emeritus Professor
Design, Manufacturing and Engineering Management
Back to staff profile
Prize And Awards
- Best Poster (Application) Award
- Recipient
- 21/6/2017
- University of Strathclyde Knowledge Exchange Award
- Recipient
- 2014
- KTP Academic Ambassador of the year 2013
- Recipient
- 1/2013
Back to staff profile
Publications
- A novel approach towards sustainability assessment in manufacturing and stakeholder's role
- Rasheed Aamir, Ion William
- Sustainability Vol 14 (2022)
- https://doi.org/10.3390/su14063221
- Automated analysis of platelet microstructures using a feature length orientation space
- Campbell A, Murray P, Yakushina E, Borocco A, Dokladal P, Decencière P, Ion W, Marshall S
- Journal of Materials Science Vol 57, pp. 1448-1461 (2022)
- https://doi.org/10.1007/s10853-021-06630-6
- An investigation of the translational asset : a proposed classification
- Strazzullo Gennaro, Ion William J, MacBryde Jillian
- The Journal of the Knowledge Economy Vol 13, pp. 3123-3149 (2021)
- https://doi.org/10.1007/s13132-021-00816-8
- Optimisation of cutting parameters and surface deformation during thin steel sheets plasma processing using Taguchi approach
- Gani Adel, Ion William, Yang Erfu
- Advances in Mechanical Engineering Vol 13 (2021)
- https://doi.org/10.1177/16878140211030401
- Experimental investigation of plasma cutting two separate thin steel sheets simultaneously and parameters optimisation using Taguchi approach
- Gani Adel, Ion William, Yang Erfu
- Journal of Manufacturing Processes Vol 64, pp. 1013-1023 (2021)
- https://doi.org/10.1016/j.jmapro.2021.01.055
- The exploration of collaborative supply chain factors in the oil and gas industry
- Olisah Moses Chijioke, Nwankpa Chigozie, Whitfield Ian, Ion William
- BAM 2020: 34th Annual Conference of the British Academy of Management (2020)
Back to staff profile
Professional Activities
- Advanced Manufacturing & Materials Showcase
- Participant
- 21/8/2019
- IN SILICO MODEL-BASED PATIENT-SPECIFIC SOLUTION SYSTEM FOR BLEPHAROPTOSIS SURGERY
- Contributor
- 7/2019
- Scottish Science Advisory Council (External organisation)
- Advisor
- 6/2019
- 20th International Conference on Engineering and Product Design Education: Diversity or Conformity?
- Organiser
- 1/5/2018
- Faculty Robotics and Automation Users Group Discussion
- Participant
- 10/10/2017
- University Of Strathclyde (Organisational unit)
- Member
- 7/2016
Projects
- International Labour Organisation - Skills for Prosperity Project in Indonesia - PPNS
- Kurt, Rafet (Principal Investigator) Atlar, Mehmet (Co-investigator) Boon, Stuart (Co-investigator) Brennan, Feargal (Co-investigator) Demirel, Yigit Kemal (Co-investigator) Giagloglou, Eva (Co-investigator) Gunbeyaz, Sefer Anil (Co-investigator) Ion, William (Co-investigator) RAMIREZ MARENGO, Maria (Co-investigator) Riches, Phil (Co-investigator) Tezdogan, Tahsin (Co-investigator) Turan, Osman (Co-investigator)
- 27-Jan-2021 - 31-Jan-2022
- Online Delivery of Digital Manufacturing and Leadership Skills Training (AMCF)
- Ion, William (Principal Investigator) Campbell, Andrew John (Co-investigator) Hernandez, Jose Luis (Co-investigator)
- 01-Jan-2020 - 30-Jan-2023
- Developing the skills system for the National Manufacturing Institute for Scotland (NMIS)
- Anderson, Pauline (Principal Investigator) Findlay, Patricia (Co-investigator) Ion, William (Co-investigator)
- 23-Jan-2019 - 22-Jan-2019
- AFRC_DIRF_1180
- Ion, William (Principal Investigator)
- 01-Jan-2018 - 30-Jan-2022
- Fast-tracking Health Innovation for NHS Scotland. MRC Confidence in Concept / R180246-102
- Ion, William (Principal Investigator)
- 01-Jan-2018 - 28-Jan-2020
- Robotic Wire + Arc Additive Manufacture cell
- Pierce, Gareth (Principal Investigator) Gachagan, Anthony (Co-investigator) Ion, William (Co-investigator) MacLeod, Charles Norman (Co-investigator)
- "Additive manufacturing (AM) has gained significant interests from industries of different sectors. Among different AM processes, Wire + Arc Additive Manufacturing (WAAM), which used metal wire as feedstock and electric arc as a heat source, has been shown to be suitable for producing large scale components with comparatively low equipment cost and running cost. The WAAM process has been developed in Cranfield University for many years, many large components of different materials, including titanium alloys, aluminium alloys, nickel alloys as well as steels have been successfully built for industrial partners.
The end-user industries, such as Airbus, FMC technologies and Glemalmond Group see significant benefits presented by the WAAM process to be able to manufacture structural components in a short lead time with low cost. Kuka Systems sees the great opportunity to get the forefront of this technology and to get the business benefit from commercialisation of the first WAAM machine. The main target of this project is to develop a commercial robotic WAAM machine (ROBOWAAM) that can be used by industrial partners for building meter scale components. Cranfield University will integrate its extensive WAAM process knowledge into a feature- based path planning software to support the end-users to manufacture components for their applications. In additional an online feedback control system will be developed and integrated into ROBOWAAM machine to correct build height errors.
To assure the deposition quality of the part, in-process nondestructive testing (NDT) method needs to be applied. Usually NDT is applied after the components has been finished. It is a time consuming and costly process if a defect is found which would either require a repair procedure or may lead to scrapping of the part. Thus an in-process NDT method is required to for inspecting each layer of the deposition. If a defect is found then the current layer will need to be machined before the recommence of the deposition. Cranfield University will collaborate with the University of Strathclyde and Advanced Forming Research Centre (AFRC) on a feasibility study of the in-process NDT method on the WAAM parts with existing NDT technologies. The in-process NDT will be incorporated with the WAAM process into a parallel processing system and the capability of this system will be demonstrated in this project.
In addition, an extended study will be performed on the automation requirements of the whole WAAM chain. This will include the pre-WAAM processes such as substrate cleaning, post-WAAM process such as heat treatment and final machining, parallel processes such as in-process NDT and top surface machining, as well as material manipulation between processes." - 01-Jan-2017 - 31-Jan-2021
Back to staff profile
Contact
Professor
Bill
Ion
Emeritus Professor
Design, Manufacturing and Engineering Management
Email: w.j.ion@strath.ac.uk
Tel: Unlisted