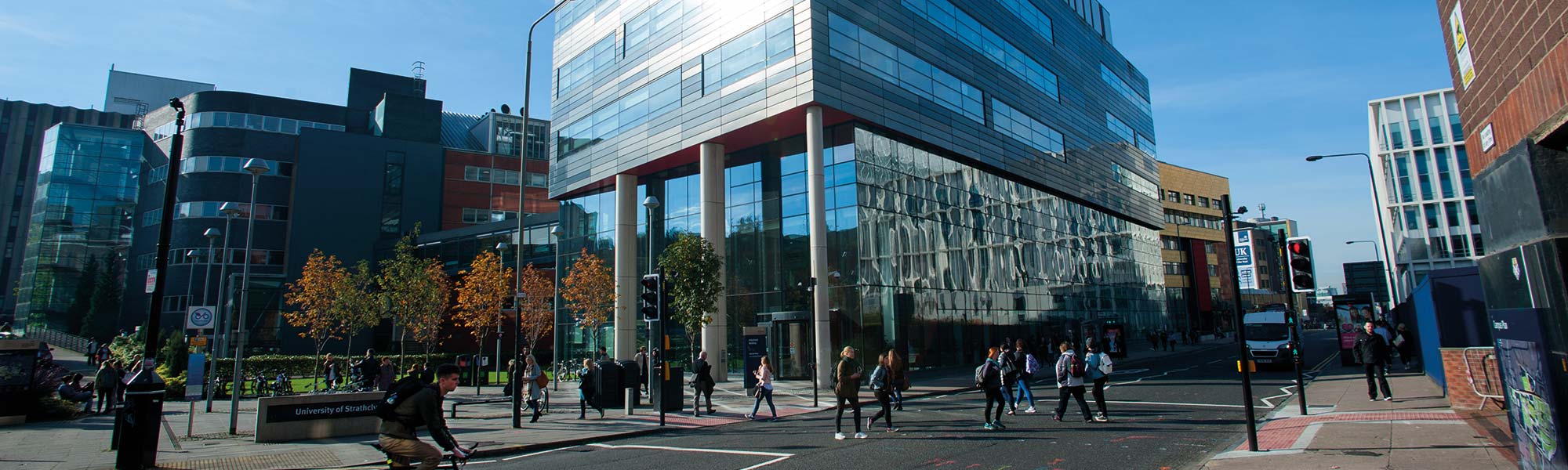
Professor Donald MacKenzie
Mechanical and Aerospace Engineering
Back to staff profile
Area of Expertise
- Finite element analysis
- Pressure Vessel Design
- Linear & non-linear analysis of structures & components
- Design by analysis assessment - elastic and inelastic
Back to staff profile
Publications
- Crack arrest analysis of components with compressive residual stress
- Xiao Xuran, Okorokov Volodymyr, Mackenzie Donald
- Fatigue and Fracture of Engineering Materials and Structures Vol 48, pp. 1272-1287 (2025)
- https://doi.org/10.1111/ffe.14539
- Calibration of the DEM sliding friction and rolling friction parameters of a cohesionless bulk material
- Marin Perez Jonatan Emanuel, Comlekci Tugrul, Gorash Yevgen, MacKenzie Donald
- Particuology Vol 92, pp. 126-139 (2024)
- https://doi.org/10.1016/j.partic.2024.05.003
- Application of finite-life frequency sensitivity evaluation methods to UFT of ferritic structural steels
- Milne Lewis Andrew, Gorash Yevgen, Comlekci Tugrul, MacKenzie Donald
- Fatigue Design 2023, pp. 365-374 (2024)
- https://doi.org/10.1016/j.prostr.2024.03.039
- High cycle fatigue analysis with induced residual stress based on fracture mechanics
- Xiao Xuran, Okorokov Volodymyr, Mackenzie Donald
- Procedia Structural Integrity Vol 52, pp. 111-121 (2024)
- https://doi.org/10.1016/j.prostr.2023.12.012
- High cycle fatigue life assessment of notched components with induced compressive residual stress
- Xiao Xuran, Okorokov Volodymyr, MacKenzie Donald
- International Journal of Pressure Vessels and Piping Vol 206 (2023)
- https://doi.org/10.1016/j.ijpvp.2023.105069
- Structural steel crack propagation experimental and numerical analysis
- Comlekci Tugrul, Marin Perez Jonatan, Milne Lewis, Gorash Yevgen, MacKenzie Donald
- European Conference on Fracture 2022, pp. 694-701 (2023)
- https://doi.org/10.1016/j.prostr.2022.12.088
Back to staff profile
Projects
- Development of Sustainable Mining Equipment using Novel Fracture Mechanics based Structural Design Optimisation SRSS REA 2725 WARC International PhD Student
- Comlekci, Tugrul (Principal Investigator) Gorash, Yevgen (Co-investigator) MacKenzie, Donald (Co-investigator)
- 01-Jan-2023 - 31-Jan-2026
- Concept feasibility for novel micro-launcher
- Maddock, Christie (Principal Investigator) Fossati, Marco (Co-investigator) Jalalvand, Meisam (Co-investigator) MacKenzie, Donald (Co-investigator) Ricciardi, Lorenzo Angelo (Co-investigator) Vasile, Massimiliano (Co-investigator) Zhou, Xingguo (Co-investigator)
- 01-Jan-2019 - 30-Jan-2020
- Tubular Sciences Initial Project
- MacKenzie, Donald (Principal Investigator)
- 01-Jan-2018 - 31-Jan-2018
- Rolls Royce Civil PhD 2
- MacKenzie, Donald (Principal Investigator) Boyle, James (Co-investigator)
- 01-Jan-2016 - 30-Jan-2020
- Rolls Royce Civil PhD 1
- MacKenzie, Donald (Principal Investigator) Boyle, James (Co-investigator)
- 01-Jan-2016 - 30-Jan-2020
- Doctoral Training Partnership (DTP 2016-2017 University of Strathclyde) | Connolly, Stephen
- MacKenzie, Donald (Principal Investigator) Gorash, Yevgen (Co-investigator) Connolly, Stephen (Research Co-investigator)
- 01-Jan-2016 - 22-Jan-2020
Back to staff profile
Contact
Professor
Donald
MacKenzie
Mechanical and Aerospace Engineering
Email: d.mackenzie@strath.ac.uk
Tel: 548 2844