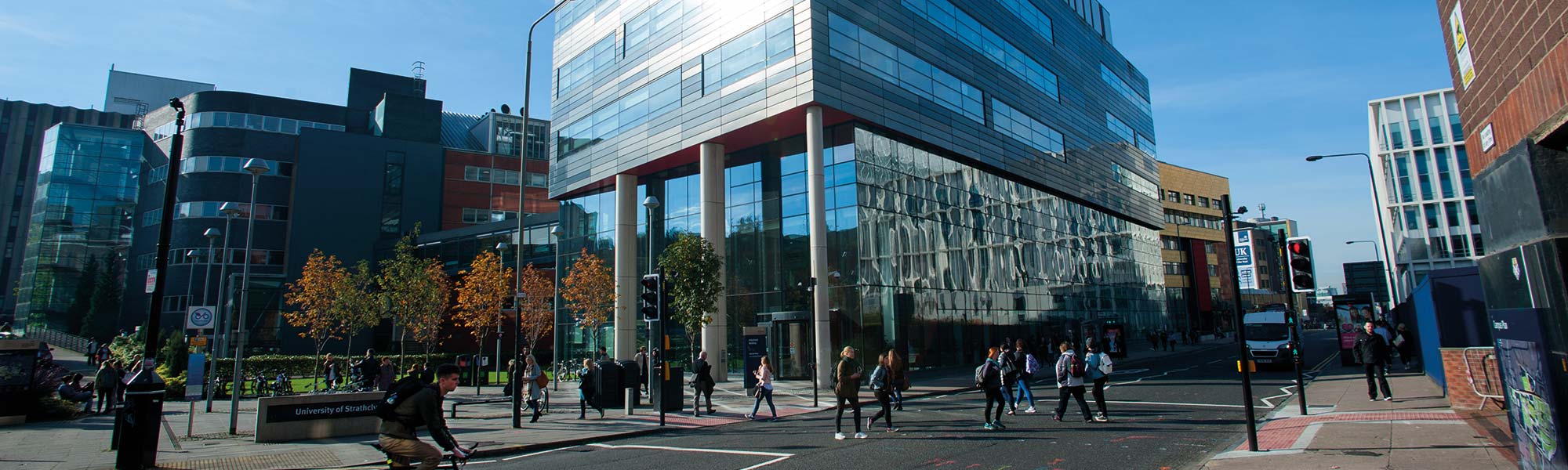
Dr Vassili Vorontsov
Senior Lecturer
Design, Manufacturing and Engineering Management
Back to staff profile
Prize And Awards
- TMS EPD science award for article on processing of nonferrous metals
- Recipient
- 2018
- President’s award for outstanding research team
- Recipient
- 2017
- Imperial College/Rolls-Royce Research Fellowship
- Recipient
- 2014
- Highly Commended Author: James Clerk Maxwell young writers prize runner up award
- Recipient
- 2013
- Faculty award for achievements and contributions to the College
- Recipient
- 2013
- EPSRC Doctoral Prize Fellowship
- Recipient
- 2012
Back to staff profile
Publications
- Miniaturised experimental simulation and combined modelling of open-die forging of Ti-6Al-4V titanium alloy
- Connolly David, Fabris Mathieu, Sivaswamy Giribaskar, Rahimi Salah, Vorontsov Vassili
- Journal of Materials Research and Technology Vol 30, pp. 3622-3639 (2024)
- https://doi.org/10.1016/j.jmrt.2024.04.084
- Miniaturised experimental simulation of open-die forging
- Connolly David, Sivaswamy Giribaskar, Rahimi Salaheddin, Vorontsov Vassili
- Journal of Materials Research and Technology Vol 26, pp. 3146-3161 (2023)
- https://doi.org/10.1016/j.jmrt.2023.08.073
- Martensitic twinning transformation mechanism in a metastable IVB element-based body-centered cubic high-entropy alloy with high strength and high work hardening rate
- Huang Yuhe, Gao Junheng, Vorontsov Vassili, Guan Dikai, Goodall Russell, Dye David, Wang Shuize, Zhu Qiang, Wrainforth Mark, Todd Iain
- Journal of Materials Science and Technology Vol 124, pp. 217-231 (2022)
- https://doi.org/10.1016/j.jmst.2022.03.005
- Precipitate dissolution during deformation induced twin thickening in a CoNi-base superalloy subject to creep
- Vorontsov Vassili A, McAuliffe Thomas P, Hardy Mark C, Dye David, Bantounas Ioannis
- Acta Materialia Vol 232 (2022)
- https://doi.org/10.1016/j.actamat.2022.117936
- Strengthening κ-carbide steels using residual dislocation content
- Kwok TWJ, Rahman KM, Vorontsov VA, Dye D
- Scripta Materialia Vol 213 (2022)
- https://doi.org/10.1016/j.scriptamat.2022.114626
- Femtosecond quantification of void evolution during rapid material failure
- Coakley James, Higginbotham Andrew, McGonegle David, Ilavsky Jan, Swinburne Thomas D, Wark Justin S, Rahman Khandaker M, Vorontsov Vassili A, Dye David, Lane Thomas J, Boutet Sébastien, Koglin Jason, Robinson Joseph, Milathianaki Despina
- Science Advances Vol 6 (2020)
- https://doi.org/10.1126/sciadv.abb4434
Back to staff profile
Professional Activities
- Materials Characterization (Journal)
- Peer reviewer
- 9/4/2025
- Materials Characterization (Journal)
- Peer reviewer
- 4/1/2025
- Scripta Materialia (Journal)
- Peer reviewer
- 4/1/2025
- PhD Viva Voce Examination - External Examiner
- Examiner
- 18/12/2024
- Henry Royce Institute (External organisation)
- Advisor
- 2/12/2024
- Communications Materials (Journal)
- Peer reviewer
- 1/10/2024
Projects
- DTP 2224 University of Strathclyde | Iwediba, Isaac Ifeanyi
- Vorontsov, Vassili (Principal Investigator) Wong, Andy TC (Co-investigator) Iwediba, Isaac Ifeanyi (Research Co-investigator)
- 01-Jan-2023 - 01-Jan-2027
- Doctoral Training Partnership 2020-2021 University of Strathclyde | Dogan, Gulsum
- Vorontsov, Vassili (Principal Investigator) Rahimi, Salaheddin (Co-investigator) Dogan, Gulsum (Research Co-investigator)
- 01-Jan-2022 - 01-Jan-2025
- Doing More With Less: A Digital Twin for state-of-the-art and emerging high value manufacturing routes of high integrity titanium alloy components
- Wynne, Bradley (Principal Investigator) Rahimi, Salaheddin (Co-investigator) Vorontsov, Vassili (Co-investigator)
- 01-Jan-2020 - 31-Jan-2024
- Industrial Case Account - University of Strathclyde 2019 | Catterson, John Conor
- Vorontsov, Vassili (Principal Investigator) Rahimi, Salaheddin (Co-investigator) Catterson, John Conor (Research Co-investigator)
- 01-Jan-2019 - 01-Jan-2024
- Industrial Case Account - University of Strathclyde 2019 / S190404-102
- Vorontsov, Vassili (Principal Investigator)
- 01-Jan-2019 - 30-Jan-2024
- Miniaturised experimental simulation of ingot-to-billet conversion
- Vorontsov, Vassili (Principal Investigator)
- Ingot-to-billet conversion processing, or "cogging", is an important production step in high-value metallurgical manufacturing. It is necessary to homogenise and refine the microstructure of high-performance alloys before they proceed to subsequent processing stages, such as hot-forging. Despite its importance, the process is still not very well understood for many modern advanced alloys and few published studies exist. The limited knowledge of the deformation and microstructure evolution leads to difficulties in achieving the desired accuracy of microstructure control. Given significant costs of large multi-tonne workpiece ingots and the difficulties with their non-destructive evaluation, it is crucial to develop a laboratory-scale evaluation for the cogging process so that scrapping and re-processing can be avoided.
Over the course of the project the student will develop automated apparatus to cost-effectively simulate cogging on a laboratory scale, whereby test specimens will be rotated in synchronous alternation with compressive deformation at elevated temperatures. A commercial high-temperature superalloy will be used for the study to help gain an improved understanding of plastic deformation during cogging and optimise the processing conditions. The student will use digital image correlation and crystal orientation mapping (electron back-scatter diffraction, EBSD) to measure how deformation is localised within the different microstructural features of the alloys. - 01-Jan-2019 - 30-Jan-2022
Back to staff profile
Contact
Dr
Vassili
Vorontsov
Senior Lecturer
Design, Manufacturing and Engineering Management
Email: vassili.vorontsov@strath.ac.uk
Tel: 548 4932