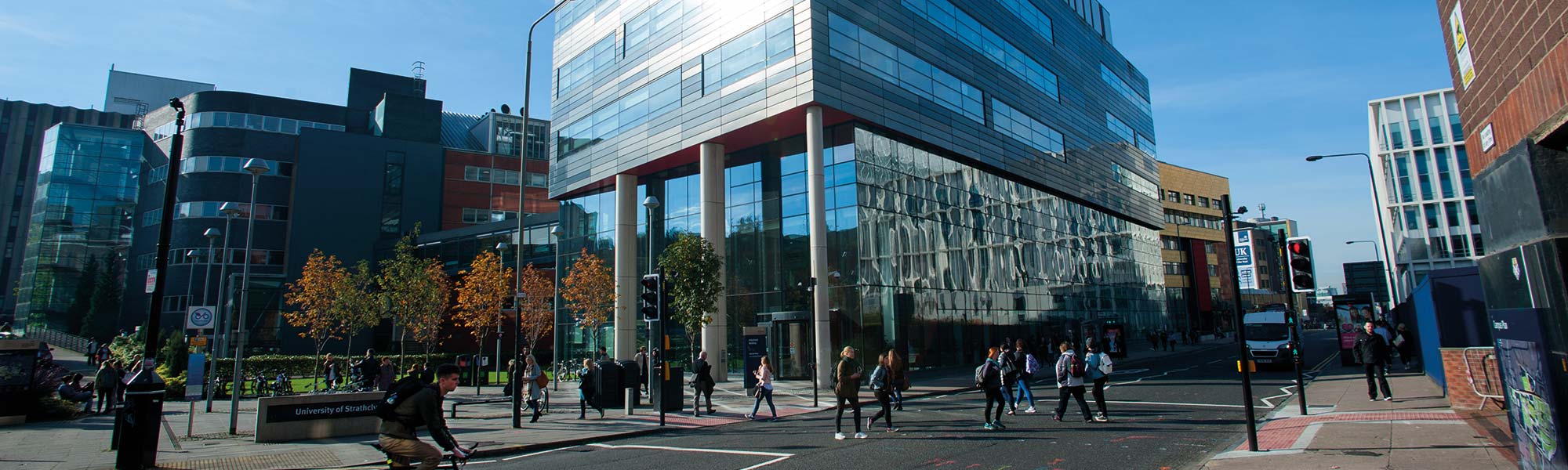
Professor Bradley Wynne
Head Of Department
Mechanical and Aerospace Engineering
Back to staff profile
Publications
- Modelling and measurements of thermally induced residual stress in IN718 nickel-based superalloy during non-uniform quenching
- Rahimi Salah, King Michael, Amir Siddiq Muhammad, Wynne Bradley
- Materials and Design Vol 250 (2025)
- https://doi.org/10.1016/j.matdes.2025.113615
- Microstructural analysis of titanium alloys based on high-temperature phase reconstruction
- Lypchanskyi Oleksandr, Muszka Krzysztof, Wynne Bradley, Kawalko Jakub, Śleboda Tomasz
- Journal of Materials Science Vol 59, pp. 18901-18915 (2024)
- https://doi.org/10.1007/s10853-024-09963-0
- Tool for automatic macrozone characterization from EBSD data sets of titanium alloys
- Fernández Silva B, Jackson M, Fox K, Wynne B P
- Journal of Applied Crystallography Vol 56, pp. 737-749 (2023)
- https://doi.org/10.1107/s1600576723003862
- The FutureForge manipulator and an approximate analytical solution algorithm for its nonlinear dynamics
- Johnston Daniel, Cartmell Matthew, Wynne Bradley, Pakrashi Vikram, Kovacic Ivana
- 10th European Nonlinear Dynamics Conference, pp. 774-783 (2022)
- Digital twins for high-value components
- Rahimi Salah, Violatos Ioannis, Wynne Bradley, Jackson Martin
- 30 (2022)
- Inter-relationship between microstructure evolution and mechanical properties in inertia friction welded 8630 low-alloy steel
- Banerjee Amborish, Ntovas Michail, Da Silva Laurie, Rahimi Salah, Wynne Bradley
- Archives of Civil and Mechanical Engineering Vol 21 (2021)
- https://doi.org/10.1007/s43452-021-00300-9
Back to staff profile
Projects
- APP13860: RTP-Led National Technical Platform for Materials Innovation
- Wynne, Bradley (Principal Investigator) King, Michael (Co-investigator)
- 01-Jan-2024 - 31-Jan-2028
- Towards Sustainable Superplastic Forming
- Wynne, Bradley (Principal Investigator)
- 01-Jan-2024 - 31-Jan-2026
- Symbolic Computation for Differential Equation Based Systems
- Cartmell, Matthew (Principal Investigator) Minisci, Edmondo (Co-investigator) Wynne, Bradley (Co-investigator)
- 01-Jan-2022 - 31-Jan-2026
- Ultrasonic Evaluation of Additively Manufactured Titanium Components
- Tant, Katherine Margaret Mary (Principal Investigator) Blackburn, Dion (Post Grad Student) Wynne, Bradley (Co-investigator)
- PhD studentship funded by the EPSRC CDT in Future UltraSonic Engineering,
Additive Manufacturing (AM) is a key driver of Industry 4.0, and has the potential to automate manufacturing of bespoke products with reduced costs, waste and energy consumption. This is of course highly desirable for companies not only in terms of profit, but in terms of sustainability and compliance with environmental targets and mandates. However, to unlock the full potential of AM in safety critical industries, it is imperative that the structural integrity of built parts is assured. Unfortunately, the lack of AM process stability, robustness and repeatability mean that it is difficult to control and predict the material properties of the built components due to the presence of defects induced by the equipment, process and/or feedstock inconsistencies. If this challenge cannot be overcome, the value of AM in high value industries is severely threatened.
To address this challenge, the development of reliable and robust in-process materials characterisation is vital. This would allow operators to adjust the AM control parameters online to compensate for any variations, or alternatively to discard poorly constructed components before they are completed, saving time, energy and money.
The central aim of this project is to develop models of ultrasonic wave propagation in the evolving microstructures of titanium alloys observed during metal additive manufacturing processes. We will examine ultrasonic propagation through both α-β phase (fig. 1a) and pure β phase (fig. 1b) structures to determine whether the larger scale β phase structures consistently dominate the effects on wave propagation (note that during the AM process, the alloy will cycle between these two states due to the applied thermal fields). These models will enhance our understanding of how ultrasound interacts with both the spatially and temporally changing microstructures, and will in turn facilitate the development of bespoke ultrasonic materials characterisation algorithms which will enable superior in-process imaging of the AM component. The student will study mathematical models of wave propagation through complex materials represented using statistical distributions, which will be informed by models of the microstructure evolution itself. These will be validated using commercial finite element modelling software. An inverse relationship between the transmitted wave forms and the descriptive statistics of the microstructure will be explored and used to monitor changes as the AM process progresses. - 01-Jan-2021 - 01-Jan-2024
- Doing More With Less: A Digital Twin for state-of-the-art and emerging high value manufacturing routes of high integrity titanium alloy components
- Wynne, Bradley (Principal Investigator) Rahimi, Salaheddin (Co-investigator) Vorontsov, Vassili (Co-investigator)
- 01-Jan-2020 - 31-Jan-2024
Back to staff profile
Contact
Professor
Bradley
Wynne
Head Of Department
Mechanical and Aerospace Engineering
Email: bradley.wynne@strath.ac.uk
Tel: 548 2322