
Net Zero Technology CentreSmart Autonomous Systems for the Visual Inspection in Harsh Environment
Project Overview
Robotic and autonomous systems (RAS) have received increasing interest both in onshore and offshore applications where the harsh environment has been a challenging issue, particularly in the oil and gas industry. Among these applications, regular visual inspection plays a key role in maintaining the proper function of industrial assets throughout their lives. The rising safety, time and cost concerns relating to the visual inspection of important industrial equipment and infrastructures are the key drivers for the deployment of robotics and autonomous systems technology. In addition, recent developments in autonomous robots have enabled machines with greater levels of flexibility and adaptability, allowing them to perform various tasks more efficiently than the human counterpart. Small, lightweight and smart RASs such as Unmanned aerial vehicles (UAVs)/drones incorporated with deep learning-based algorithms can be deployed quickly to assess the internal and external conditions are highly desirable. This project is supported by the Net Zero Technology Centre (NZTC) and the ambition of this project is to develop deep learning-based autonomous visual perception and defect detection systems to assist in performing an initial assessment of surface conditions through the use of the autonomous UAV.
Why Strathclyde
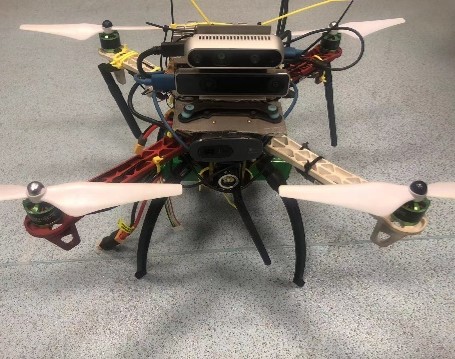
The University of Strathclyde has gained many awards, and it has a good reputation among international universities. The department of Design, Manufacturing and Engineering Management (DMEM) is a unique department in the UK that offers multidisciplinary expertise to help students. What is more, the department provided the necessary equipment to support students’ projects. For my project, I can access the UAV and accessories from the Robotics & Autonomous Systems Research Group. What is more, it offers the opportunity of transferring the concept we developed into a product prototype. Through carrying out the project with the support of the industry, I have experienced the whole process of developing an entire system, as well as the way of project management. Besides, the university is in the centre of Glasgow, which welcomes people from all over the world. The university also offers a cultural inclusion environment to support students from different nationalities. Moreover, everyone is approachable, and students can experience different cultures during their research at the university.
Researcher Experience
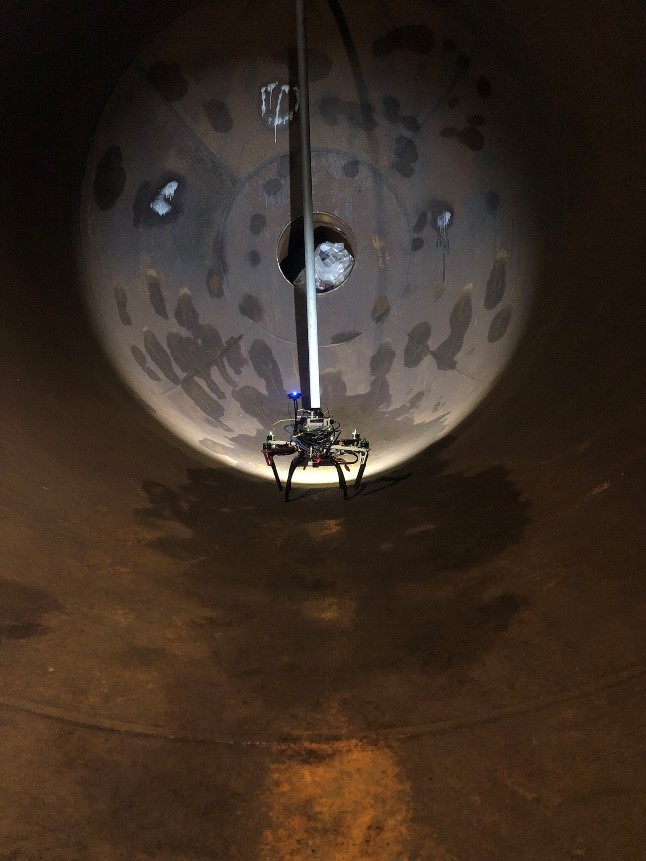
Through the cooperation with the NZTC, I have the chance to discuss with the visual inspection engineer directly. It saves my time to understand their needs in detail and construct a solid background understanding of the visual inspection. During the platform development procedure, the industry assisted my project by providing the industrial observation suggestions, datasets and prototype testing fields. With their help, my consideration covered more aspects when designing and developing the perception and detection system for the robotic visual inspection platform. Moreover, I have also received periodic feedback from the industrial partner to refine the developed system. With the engagement with the company, I could make the theory I developed to practice. During this process, I have had a deeper understanding of the developed algorithms. Meanwhile, the effectiveness of the developed systems was also verified through the field test, and I have gained some basic observations about project management. The technical and management skill I learned from the collaboration with the NZTC will benefit my future career a lot.
Business Impact

A novel UAV-assisted visual inspection system was developed by the end of the project, which can significantly impact the operation by improving the inspection efficiency. The adoption of deep learning-based methods into the physical visual inspection solution enhanced the robustness and accuracy of robotic inspection systems in business operation. This project tightly linked the university and industry and offered a robotic platform to deploy the advanced algorithms to support the industrial visual inspections with potential wide applications. With the deep learning-based visual localisation system, the UAV could fly stably in a complex environment such as poor or low illuminations. With the proposed deep learning-based accurate corrosion detection system, the UAV could identify the defects autonomously to further improve the visual inspection efficiency. This project developed the prototype of the autonomous UAV for visual inspection of pressure vessels which is a hazardous environment for engineers. In the final demonstration, the feasibility of deploying the autonomous UAV to inspect facilities with high efficiency and safety was confirmed.