The Business Improvement Team recently had the privilege of facilitating a Five Day Rapid Improvement Event with University of Strathclyde’s Advanced Forging Research Centre (AFRC) which is based at Inchinnan near to Glasgow Airport.
The AFRC is a collaborative venture between the University of Strathclyde, Scottish Enterprise, the UK Government and leading multinational engineering firms. The £35million facility focuses on developing forming and forging technologies to support the development of high integrity components.
So what did the Rapid Improvement Event involve?
Day 1: Lean Training and High Level Mapping
Day 2: Understanding the Current Condition and Wastes in the Process
Day 3: Improvement Idea Generation and the Future State
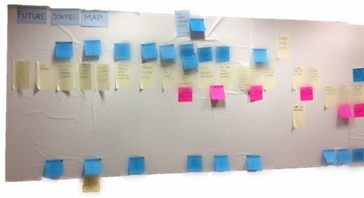
Day 4: Implementing Solutions
Day 5: Communicating Outcomes and Sustainment Planning
Throughout the event the team had formally communicated with the Team Leaders and Directors at the AFRC with updates on a daily basis. On the final day, with everyone in attendance, a wrap up presentation took place to summarise the outcomes from the event, and an outline of the next steps. The team achieved some potentially significant step change improvements in just a week.
Thanks to all of our colleagues at AFRC for making this a memorable Rapid Improvement Event, with excellent participation, enthusiasm and a passion to make improvements.