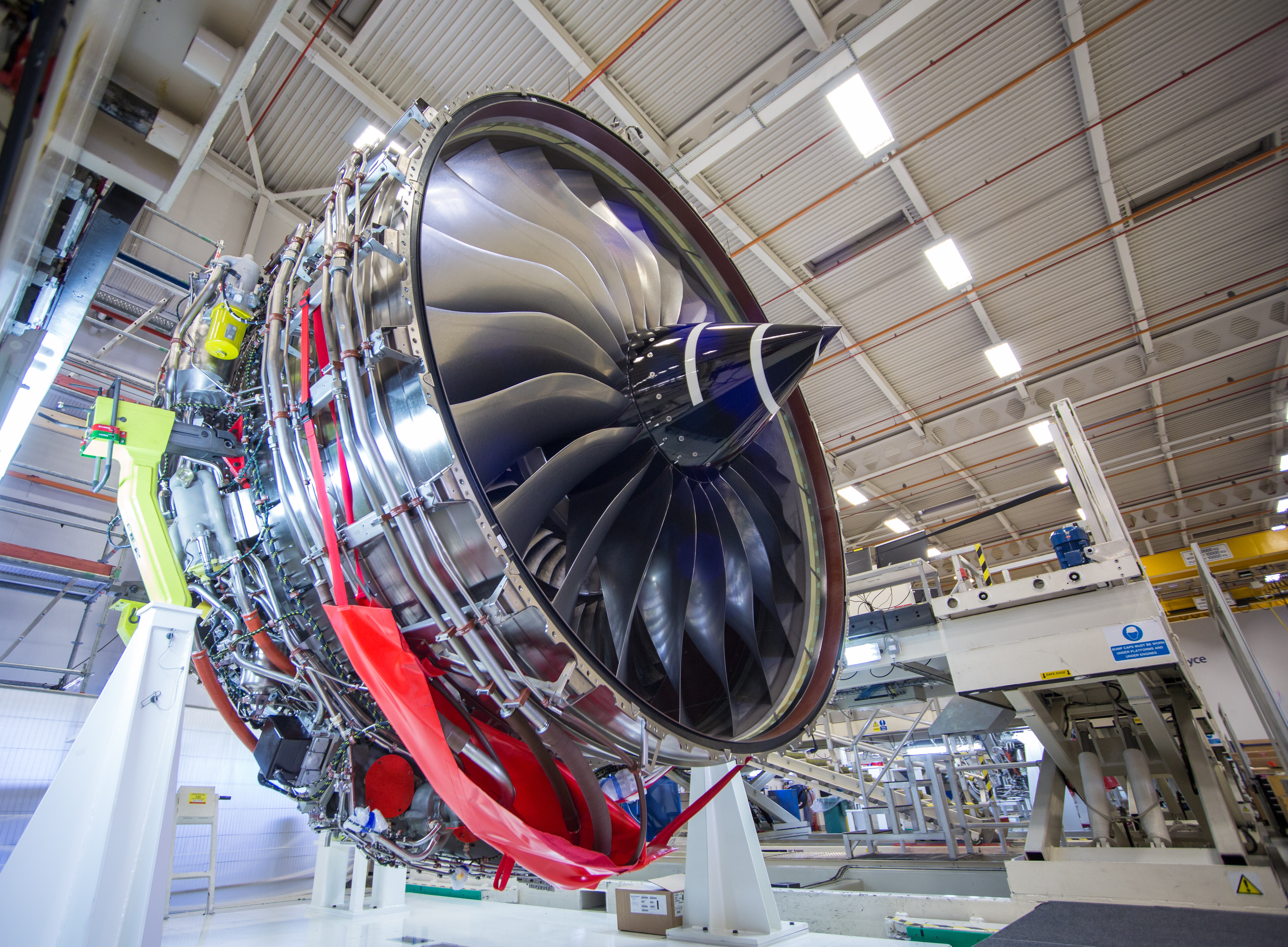
Aubert & DuvalRecrystallisation and precipitation during forging of a nickel based superalloy
Project Overview
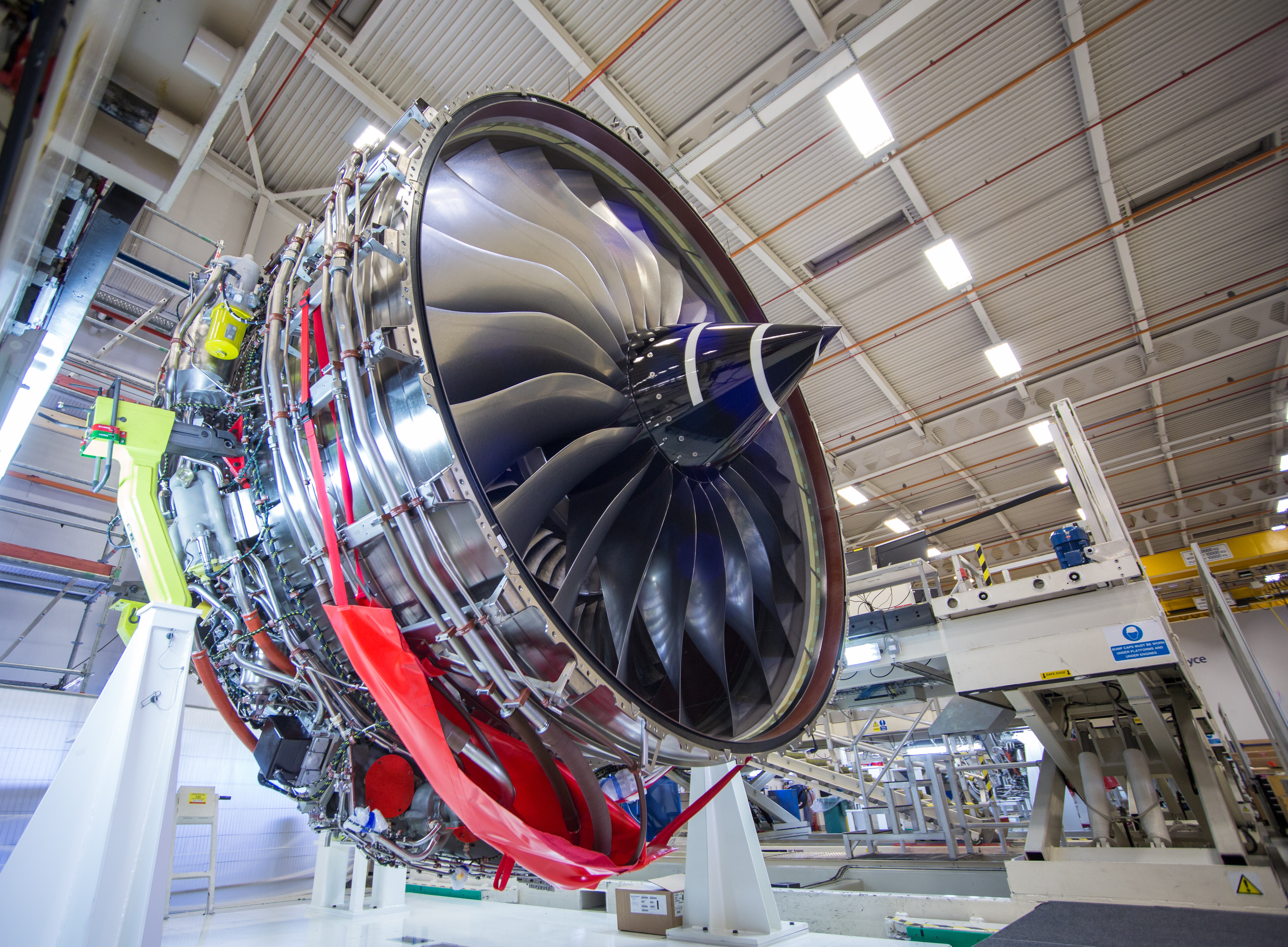
To have the right shape and internal structure, metallic components have to be forged during their fabrication. While a blacksmith might do this using a fire and a hammer, on the industrial scale furnaces operating at 1200 °C and dies exerting loads of 4,500 tonnes are more common.
Aubert & Duval produce safety critical components for plane engines, such as turbine discs, which have to operate in very challenging conditions. These parts are made from a family of alloys called nickel based superalloys. These superalloys are capable of withstanding temperatures close to 1000 °C, repeated thermal and mechanical stresses, and resist oxidation even at high temperatures.
To be confident that these critical parts will be able to operate in the challenging environment of a jet engine, their internal microscopic structure has to be controlled. The interlocking crystals (called grains) which make up the alloy must have a suitable size and level of stored energy. Additionally, the size and distribution of precipitates which form within these grains must be controlled.
My PhD examines in detail how the internal structure of a superalloy (called AD730) evolves during this industrial forging process.
Why Strathclyde
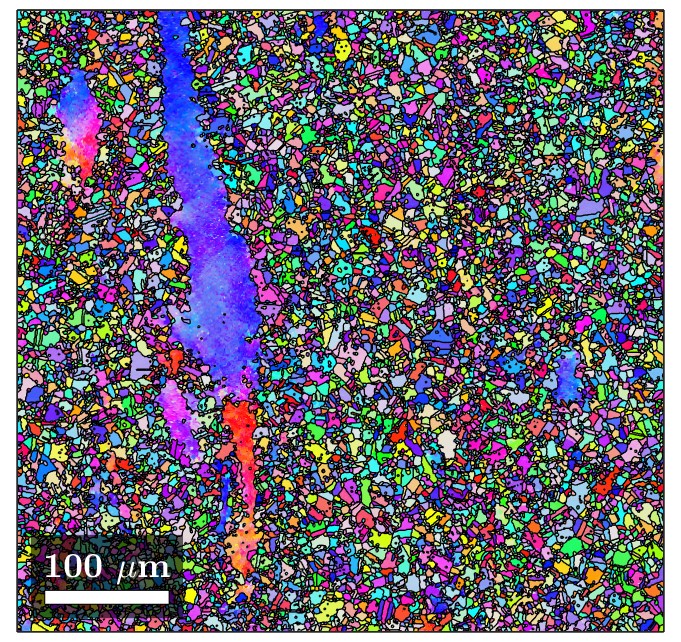
Working at the Advanced Forming Research Centre (AFRC) has been very beneficial. The mixture of academic and industry projects at the centre means it has expertise and equipment beyond what is typical in an academic setting. Working here also gives additional exposure to ‘real world’ problems faced by companies, and the work being done to address them. Such real world problems are often not purely technical, and related to funding, management, supply chains etc. Exposure to such considerations might not be as common in PhD centres which have less close contact with industry.
It is also possible to benefit from the breadth of expertise and equipment across departments and buildings. For example, I have been able to access an electron microprobe analyser operated by the physics departments at the Technology and innovation centre.
Researchers Experience

Working with an industrial partner gave me opportunities which I wouldn’t have had in a standard PhD. Most notably, I was able to travel to Les Ancizes in France to one of their manufacturing sites, and see their industrial forging process. I was also able to talk to people working directly in manufacturing, as technicians, engineers and research directors on this site, giving me a wide overview of how my research might be implemented at different levels in “the real world”.
The experience of working with a large company was also beneficial for my personal effectiveness. I have collaborated with people with diverse backgrounds, skillsets and priorities. This exposure has helped me learn to communicate more effectively, and collaborate more productively. In an academic environment colleagues tend to have more homogenous knowledge and skillsets.
Aubert & Duval have links with other academics and research centres, meaning I was able to be supervised by Prof. Bozzolo from the CEMEF in France, and was able to go to this centre for a training course, and to use their FIB-SEM nano-tomography facility, which I could not otherwise have accessed.
Business Impact
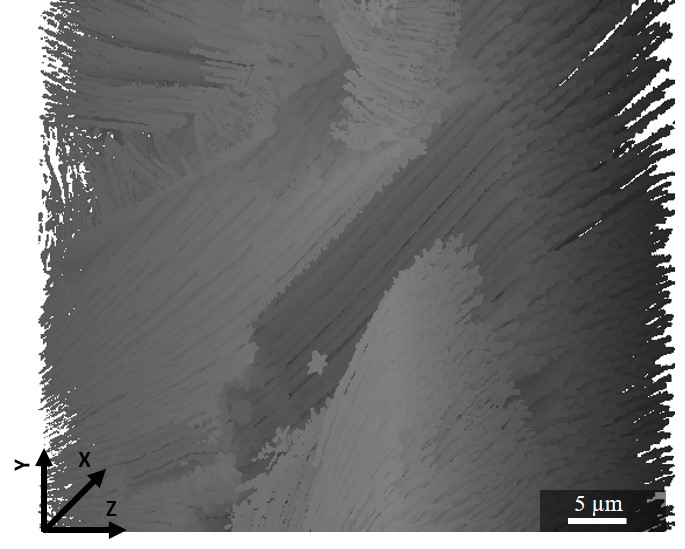
The results from this PhD have informed decisions we make about our industrial practice, and allowed us to validate and deepen our own internal research. The results from the PhD have added fundamental understanding about how the microstructure of our parts evolve during manufacture.
The PhD has allowed us to further investigate previous researches which may be incomplete, or which have not transferred from the academic to the industrial scale. We have been able to design experiments to address specific aspects of our industrial forging route.
Working with PhD students at the AFRC gives us access to additional equipment and expertise which is not as available on the industrial side, such as wavelength dispersive spectroscopy for accurate chemical analysis, and electron backscatter diffraction to examine in detail grain structures.